Home »
Accessories
»
Garments Manufacturing
»
regular
»
How to Decorate a Garment? | Fabric/Garment Decoration Techniques
How to Decorate Apparel?
Decorating Garments: Garments are decorated based on the end usage by affixing sequins, rhinestones, embroidery etc. to enhance the appearance of the final products. Whether you are selling it or thinking of producing it yourself, the technology behind the decoration will play an important part in your sales strategy and the more you know the better. In fact, selling decorated apparel without a basic understanding of the production processes could be costing you money. From a technical perspective, your knowledge of what can and cannot be produced by each different method will go a long way in how you deal with your customer’s needs. At the same time, you will be able to avoid costly mistakes (in terms of money and lost accounts) by promising things that simply aren’t possible. From a creative perspective, the more you know about the exciting array of apparel decoration processes, the better, as it will put you in a position to show your customers new concepts and looks, that can set you apart from your competition. This in turn will ultimately bring more business your way. Anybody can sell a white polo shirt with an embroidered logo, but what about a polar fleece vest with the same logo done via laser etching or perhaps a denim jacket with a chenille version? Types of Fabric/Garment Decoration Techniques: - Embroidery
- Appliqué
- Bias trimmings
- Ric rac
- 3D Foam
- Sequins
- Ruffles
- Smocking
- Faggoting
- Chenille Embroidery
- Lace
- Lace motifs
- Heat Transfers
- Belts and bow
- Decorative fasteners
- Laser Etching
- Pockets
- Scalloped edging
- Screenprinting
- Direct To Garment Printing (Digital Printing)
- Rhinestones
1. Embroidery: Simple embroidery designs enhance the appearance of children’s garments. In the dress design chain stitch for couching stitch can been worked to small motifs with lazy daisy stitches or bullion stitches are worked within the false yoke and godet. Instead of embroidery, beads or sequins can be applied. 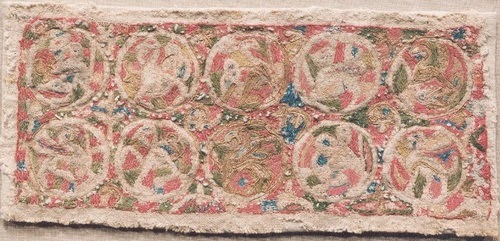 |
Embroidery |
Embroidery is normally priced by the number of stitches in a design and prices are usually quoted in “cost per thousand stitches.” More stitches means more time to produce and of course a bigger price tag. There are two key requirements for embroidering any given item: - You must be able to get a needle through it.
- You must be able to get it into a hoop or frame.
Situations to avoid with embroidery: - Very small lettering and detail. Letters below ¼” in height are tough to sew properly.
- Large designs. High stitch counts are pricey due to the production time.
- Flimsy garments. Embroidery quality is affected by garment quality.
- Stiff rigid fabrics. They may not be hoop‐able.
- Layered items. A pocket for example, as the embroidery process may sew it closed.
2. Applique: Applique is a cutout piece of fabric that is stitched to a larger background for decoration. This is a popular way of decorating fabrics. Shapes of one fabricare applied to the surface or background of another fabric using a fine zigzagstitch or as in the example shown, with a straightstitch, which overlaps the edge of each shape. Thepattern pieces that make up the appliqué are usuallybacked with interfacing to give them strength. 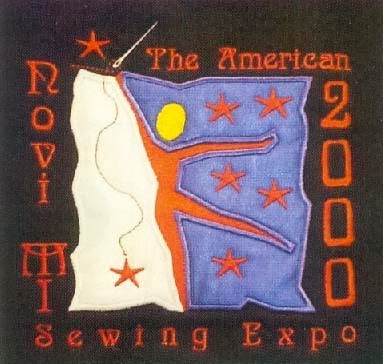 |
Applique |
The appliqué “look” is very popular with sports and school designs. The process can be used to add “tackle twill” letters, numbers and designs to garments. 3. Bias trimmings: Bias binding in contrasting material or self fabric can be used to finish neck lines, opening and hems in garments. Bias tubing can be used for making decorative button loops. 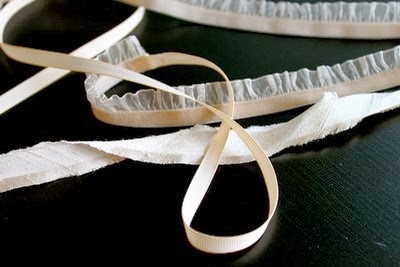 |
Bias trimmings |
4. Ric rac: This is available in different colors at very low cost and is very durable. (It should be tested for color fastness before attaching to garment). Ric rac can be sewn flat on the garment through the centre or it may be attached around edges or between seams so that just one edge is show on the right side of the garment. A motif made of ric rac adds further decoration. 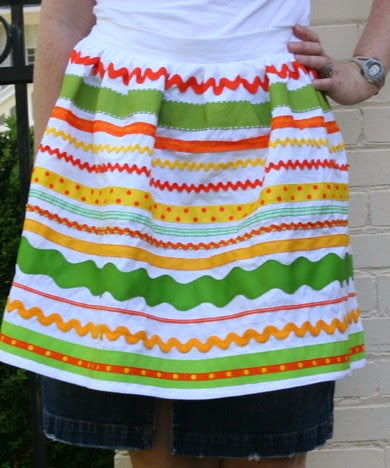 |
Ric rac |
5. 3D Foam Embroidery 3D Foam embroidery is a relatively simple process that any embroiderer has the capability of producing though it does require some special techniques during the digitizing process. The application is created by introducing a piece of foam material into the sewing process. The stitches penetrate and lock the foam into the design such that specific elements of the logo are significantly raised up above the rest of the design. 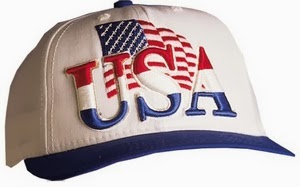 |
3D Foam Embroidery |
6. Sequin Embroidery
Sequins are starting to make an impact on the imprinted sportswear market. Long relegated to sparkly theatrical garments, sequins (or spangles) are now appearing on more mainstream products, from retail to souvenir. Of course, the applications are still limited due to the nature of the “look”, but there are still plenty of possibilities. This technique can be used on just about any design and garment, provided the Embroiderer makes the necessary adjustments during the digitizing process to accommodate the physical piece of foam. 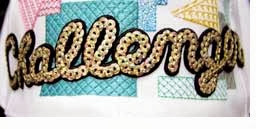 |
Sequin Embroidery |
7. Ruffles: This is also a type of frill. To make a pattern for circular ruffle. Cut a piece of circular fabric with its inner circle equal to the circumference of the neckline and its outer circle 1”- 2” away from the inner circle. Cut the circular fabric at any one point and attach it the inner circle to the neckline of the garment. Double ruffle can be attached to the armhole hemline on either sides. The placement of the double ruffle gives a panelled effect to the front of the garment. 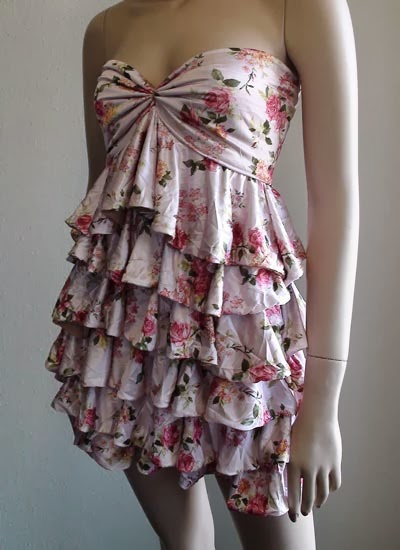 |
Ruffles |
8. Smocking: This is done by gathering and embroidering over the gathers. This can be worked only over a plain cloth. When this is done with practice this looks attractive. After knotting the thread work running stitches from right to left of equal width. Gather the fabric and wind it over the pin head. Then work desired stitch over the gathered fabric. This is used to decorate waistline, sleeve, neckline, Yoke and any other part of the garment. This stitch looks attractive and liked by many of them. 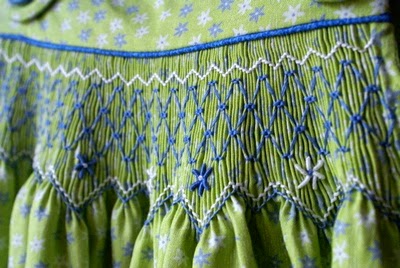 |
Smocking |
9. Faggoting: This trim is used between seams to give a decorative touch or to add the length or width of garment. To executive the design cut the yoke and the lower section of the blouse separately, with ½” seam allowances. Also cut the yoke pattern on heavy paper with one inch allowance. Fold under the allowance on edge of the yoke where faggoting is to be done and tack the folded edge to the prepared pattern. Now tack also the lower section of the blouse after folding in the seam allowance Then do the faggoting with zigzag stitches between foldings. 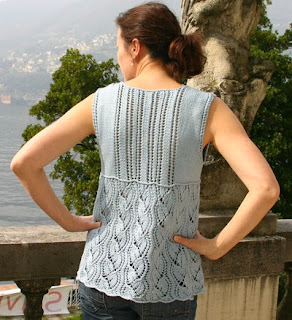 |
Faggoting |
10. Chenille Embroidery Though its technically called chenille embroidery, the process is not done with traditional embroidery machines, rather it takes special equipment to sew chenille. The application is best known for creating the “letters” on letterman jackets and the product looks kind of like an old‐style shag carpet. However, chenille has burst‐forth from the school market and is now appearing on corporate and souvenir garments with increasing frequency. 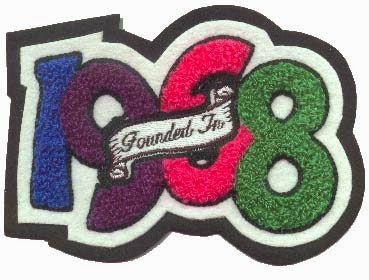 |
Chenille Embroidery |
11. Lace: Lace can be used as edging, insertion and banding. Lace for edging has one straight edge which is to be applied to the fabric. It is commonly used at the neckline, armhole, sleeve hem, garment hem, yoke line etc. Lace may be gathered to give a frilled effect. Lace for insertion has its two edges finished symmetrically. A design with fine tucks and insertion of lace can be combined and applied in a horizontal direction. The bias tubing inserted in such lace can be tied into a bow. The tubing may also be pulled to produce gathers. An attractive band can be made by placing lace over contrasting or self colored ribbon or fabric slightly narrower than the lace. The ribbon is then attached to the garment in the desired portion. 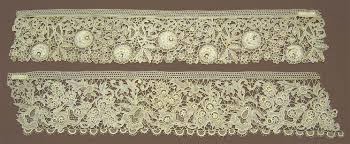 |
Lace |
12. Lace motifs: Lace motifs are very effective when sewn over contrasting fabric. The motifs can be cut out from a wide lace or bought as such. Cut the outline of the motif in a contrasting colored lining fabric and tack it to the wrong side of the lace motif. Trim the lining fabric slightly smaller around the edge. Now, applique the lined motif on the garment in the desired place. 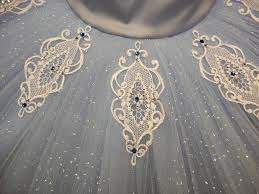 |
Lace motifs |
13. Heat Transfers Heat transfers have long been a quick method to apply printed designs to garments. Instead of creating the image directly via screenprinting or DTG, it’s created on a special paper that allows the image to transfer onto the garment when heat is applied. 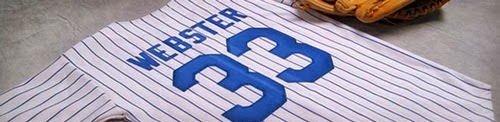 |
Heat Transfers |
14. Belts and bow: These have functional and decorative uses. In children’s garments. fabric belts are most commonly used. Belts may be made out of contrasting material or the garment material it self. The belt may be tied with a bow at the back or at one side. Bows may be attached near the neckline, shoulder, hemline, along the centre front line etc. 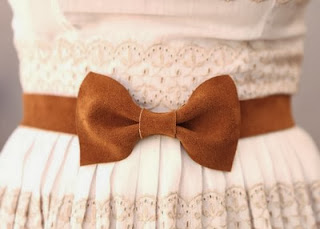 |
Belts and bow |
15. Decorative fasteners: Decorative fastenings include fabric buttons and loops eylets and cord, fancy buttons, fabric buttonholes etc. On a plain dress with contrasting collar or piping, buttons covered with the collar piping material would be effective. Buttons may be fixed in groups to create design interest gradually progressing in size from small to big. 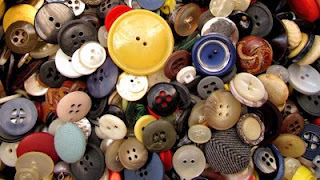 |
Decorative fasteners |
16. Laser Etching In Hollywood movies lasers are used to destroy things with awesome, spectacular results. In real life, they are typically used for precise detailed applications that require a lot of finesse, such as Lasik surgery for vision correction. Lasers have also found their way into the world of imprinted sportswear and can be used to create some amazing designs in a format not replicated by any other apparel decoration methodology. By using a precision beam of energy moving at a high speed, designs can be uniquely burned into a wide variety of fabrics without causing any harm to the garment. The process actually removes a fine layer, leaving a sort of tone‐on‐tone image behind. 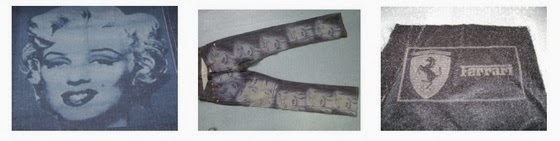 |
Laser Etching |
17. Pockets: Pockets of different shapes, sizes and location with or without decorative details suited to the design of the garment can enhance the appearance of the garment. 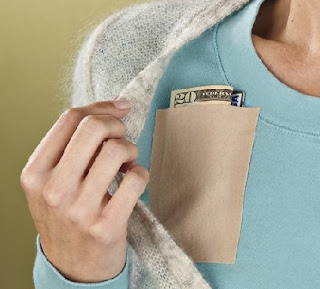 |
Pockets |
18. Scalloped edging: Scalloped shapes at garment edges (neckline, hemline openings etc.) are ordinarily made by cutting in the desired shape and finishing with bias binding or shaped facing. A similar effect may be produced however by the use of embroidery stitches. The effect of a scalloped front opening is obtained by drawing the scallops in uniform shape and working blanket stitch with contrasting colored thread along the lines drawn. This can be used in frocks, skirt, kids wear, neckline, sleeve and in table cloth. 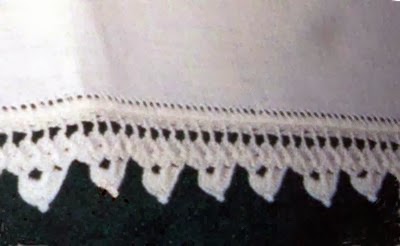 |
Scalloped edging |
19. Screen printing Screen printing has been around for ages and is the quickest and cheapest process for applying large detailed designs to a variety of garments. 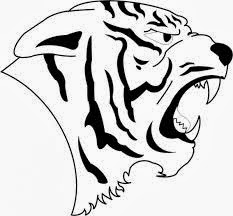 |
Screen printing |
The process is simple and complex at the same time. The first step is to breakdown the artwork by color – referred to as “color separations.” Then a separate screen composed of a very fine mesh material is created or for each color separation. The screen will only allow ink to pass through in the areas defined by that color of the design. Screens are created using a special photographic process which is referred to as “burning” by most shops. 20. Direct‐To‐Garment Printing/Digital Printing: Relatively new on the scene, direct‐to‐garment printing (DTG) – also known as digital printing – is a quick and easy method to print designs directly on garments using an oversized ink jet printer designed specifically for this purpose. Unlike screenprinting, no color separations and screen creation is required. Theoretically, it’s just point, click and print – though nothing is really that easy. 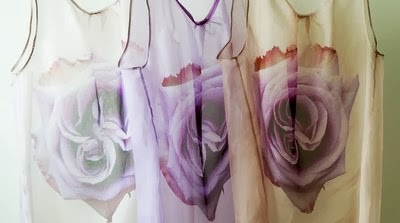 |
Digital printing |
21. Rhinestones:Much like sequins, rhinestones have traditionally appeared on garments used in the entertainment business, with a goal of adding glitz and bling to theatrical garb. But rhinestones are finding new applications in a wide range of markets. 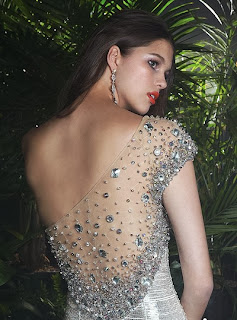 |
Rhinestones |
No Responses to "How to Decorate a Garment? | Fabric/Garment Decoration Techniques"