Sohel Hossain
B.Sc in Textile Engineering
The People’s University of Bangladesh
POLYESTER FIBERS:
Polyester fiber is a ” manufactured fiber in which the fiber forming substance is any long chain synthetic polymer composed at least 85% by weight of an ester of a dihydric alcohol (HOROH) and terephthalic acid (p-HOOC-C6H4COOH)” [3]. The most widely used polyester fiber is made from the linear polymer poly (ethylene terephtalate), and this polyester class is generally referred to simply as PET. High strength, high modulus, low _shrinkage, heat set stability, light fastness and chemical resistance account for the great versatility of PET. 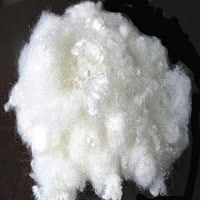 |
Fig: Polyester fiber |
Process Flow Chart Of Synthetic Fiber Production: The process flow chart of various synthetic fibers is differing from one to another but basic process is same. Here, I have given a flow chart of synthetic fiber production which is same for all. It is the basic sequence of man made fiber production. Raw Materials / monomers
↓
Polymerization
↓
Drawing and Stretching
↓
Texturing
↓
Intermingling
↓
Heat Setting
↓
Finished Filaments
Raw Materials: Polyester is a chemical term which can be broken into poly, meaning many, and ester, a basic organic chemical compound. The principle ingredient used in the manufacture of polyester is ethylene, which is derived from petroleum. In this process, ethylene is the polymer, the chemical building block of polyester, and the chemical process that produces the finished polyester is called polymerization. POLYMER FORMATION: Polyethylene Teraphthalate (PET) is a condensation polymer and is industrially produced by either terephthalic acid or dimethyl terephthalate with ethylene glycol. [26] Other polyester fibers of interest to the nonwovens field include: 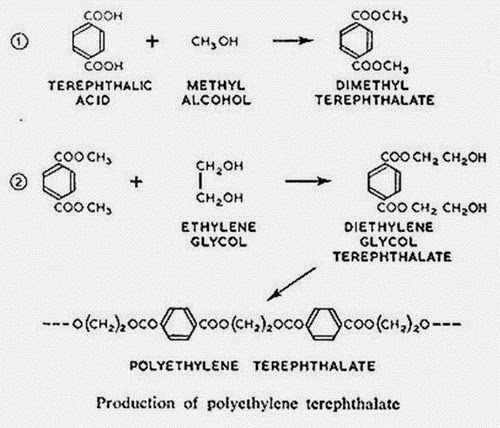 |
Fig.1: Production of polyethylene terephthalate |
(a) Terephthalic Acid (PTA), produced directly from p-xylene with bromide-controlled oxidation. (b) Dimethyl Terephthalate (DMT), made in the early stages by esterification of terephthalic acid. However, a different process involving two oxidation and esterification stages now accounts for most DMT. (c) Ethylene Glycol (EG) initially generated as an intermediate product by oxidation of ethylene. Further ethylene glycol is obtained by reaction of ethylene oxide with water. SYNTHESIS OF POLYMER: Linear Polyesters: A representative linear polyester, PET is polymerized by one of the following two ways: Ester Interchange: Monomers are diethyl terephtalate and ethylene glycol. Direct Etherification: Monomers are terephthalic acid and ethylene glycol. Both ester interchange and direct esterification processes are combined with polycondensation steps either batch-wise or continuously. Batch-wise systems need two-reaction vessels- one for esterification or ester interchange, the other for polymerization. Continuous systems need at least three vessels - one for esterification or shear interchange, another for reducing excess glycols, the other for polymerization. Another way to produce PET is solid-phase polycondensation. In the process, a melt polycondensation is continued until the pre-polymer has an Intrinsic Viscosity of 1.0-1.4, at which point the polymer is cast into a solid firm. The pre-crystallization is carried out by heating (above 200oC) until the desirable molecular weight is obtained. Later the particulate polymer is melted for spinning. This process is not popular for textile PET fibers but is used for some industrial fibers. Branched and Crosslinked Polyesters: If glycerol is allowed to react with a diacid or its anhydride each glycerol will generate one branch point. Such molecules can grow to very high molecular weight. If internal coupling occurs (reaction of a hydroxyl group and an acid function from branches of the same or different molecule), the polymer will become crosslinked. Rigidly crosslinked polymers are totally unaffected by solvents. FIBER FORMATION: The sequences for production of PET fibers and yarns depend on the different ways of polymerization (continuous, batch-wise, and solid-phase) and spinning (low or high windup speed) processes. The Manufacturing Process: Polyester is manufactured by one of several methods. The one used depends on the form the finished polyester will take. The four basic forms are filament, staple, tow, and fiberfill. In the filament form, each individual strand of polyester fiber is continuous in length, producing smooth-surfaced fabrics. In staple form, filaments are cut to short, predetermined lengths. In this form polyester is easier to blend with other fibers. Tow is a form in which continuous filaments are drawn loosely together. Fiberfill is the voluminous form used in the manufacture of quilts, pillows, and outerwear. The two forms used most frequently are filament and staple. Manufacturing of Filament Yarn: Polymerization 1 To form polyester, dimethyl terephthalate is first reacted with ethylene glycol in the presence of a catalyst at a temperature of 302-410°F (150-210°C). 2 The resulting chemical, a monomer (single, non-repeating molecule) alcohol, is combined with terephthalic acid and raised to a temperature of 472°F (280°C). Newly-formed polyester, which is clear and molten, is extruded through a slot to form long ribbons. Drying 3 After the polyester emerges from polymerization, the long molten ribbons are allowed to cool until they become brittle. The material is cut into tiny chips and completely dried to prevent irregularities in consistency. Melt spinning 4 Polymer chips are melted at 500-518°F (260-270°C) to form a syrup-like solution. The solution is put in a metal container called a spinneret and forced through its tiny holes, which are usually round, but may be pentagonal or any other shape to produce special fibers. The number of holes in the spinneret determines the size of the yarn, as the emerging fibers are brought together to form a single strand. 5 At the spinning stage, other chemicals may be added to the solution to make the resulting material flame retardant, antistatic, or easier to dye. Drawing the fiber 6 When polyester emerges from the spinneret, it is soft and easily elongated up to five times its original length. The stretching forces the random polyester molecules to align in a parallel formation. This increases the strength, tenacity, and resilience of the fiber. This time, when the filaments dry, the fibers become solid and strong instead of brittle. 7 Drawn fibers may vary greatly in diameter and length, depending on the characteristics desired of the finished material. Also, as the fibers are drawn, they may be textured or twisted to create softer or duller fabrics. Winding 8 After the polyester yarn is drawn, it is wound on large bobbins or flat-wound packages, ready to be woven into material.Manufacturing Staple Fiber: In making polyester staple fiber, polymerization, drying, and melt spinning (steps 1-4 above) are much the same as in the manufacture of filament yarn. However, in the melt spinning process, the spinneret has many more holes when the product is staple fiber. The rope-like bundles of polyester that emerge are called tow. Drawing tow 1 Newly-formed tow is quickly cooled in cans that gather the thick fibers. Several lengths of tow are gathered and then drawn on heated rollers to three or four times their original length. Crimping 2 Drawn tow is then fed into compression boxes, which force the fibers to fold like an accordion, at a rate of 9-15 crimps per inch (3-6 per cm). This process helps the fiber hold together during the later manufacturing stages. Setting 3 After the tow is crimped, it is heated at 212-302°F (100-150°C) to completely dry the fibers and set the crimp. Some of the crimp will unavoidably be pulled out of the fibers during the following processes.Cutting 4 Following heat setting, tow is cut into shorter lengths. Polyester that will be blended with cotton is cut in 1.25-1.50 inch (3.2-3.8 cm) pieces; for rayon blends, 2 inch (5 cm) lengths are cut. For heavier fabrics, such as carpet, polyester filaments are cut into 6 inch (15 cm) lengths. Spinning Process: The degree of polymerization of PET is controlled, depending on its end-uses. PET for industrial fibers has a higher degree of polymerization, higher molecular weight and higher viscosity. The normal molecular weight range lies between 15,000 and 20,000. With the normal extrusion temperature (280-290oC), it has a low shear viscosity is 1000-3000 poise. Low molecular weight PET is spun at 265oC, whereas ultrahigh molecular weigh PET is spun at 300oC or above. The degree of orientation is generally proportional to the wind-up speeds in the spinning process. Theoretically, the maximum orientation along with increase in productivity is obtained at a wind-up speed of 10,000m/min. Although due to a voided skin, adverse effects may appear at wind-up speeds above 7000m/min. Drawing Process: To produce uniform PET, the drawing process is carried out at temperature above the glass transition temperature (80-90oC). Since the drawing process gives additional orientation to products, the draw ratios (3:1-6:1) vary according to the final end-uses. For higher tenacities, the higher draw ratios are required. In addition to orientation, crystallinity may be developed during the drawing at the temperature range of 140-220oC. Polyester Fiber Flow Chart: 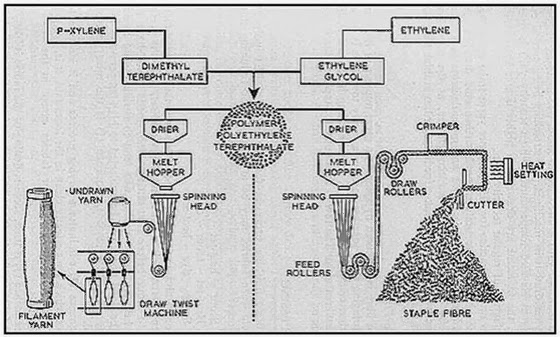 |
Fig. 2: Polyester fiber flow chart |
The latest Polyester production (Research Method): Dr Boncella and Dr Wagner at The University of Florida are two scientists involved with the study to reveal a method for manufacturing polyester from two inexpensive gases: carbon monoxide and ethylene oxide. The polyester most commonly used today is referred to as PET or polyethylene terephtalate. Scientists have been successful in producing low molecular weight polyester using carbon monoxide and ethylene oxide, but researchers still lack the catalyst - a substance that speeds up chemical reactions - needed to make the reaction work more efficiently. They are looking for the chemical compound that will take molecules of low DP and create 1arger ones. Although they have had success in the research so far, they have yet to produce commercially useable polyester from the inexpensive gases. If this is successful, then these research findings can be used to replace the current polyester product, getting the same performance for a lower price. Finally, we all know that research requires patience and a long-term effort. STRUCTURAL COMPOSITION OF PET: The one of the distinguishing characteristics of PET is attributed to the benzene rings in the polymer chain. The aromatic character leads to chain stiffness, preventing the deformation of disordered regions, which results in weak van der Waals interaction forces between chains. Due to this, PET is difficult to be crystallized. Polyester fibers may be considered to be composed of crystalline, oriented semi crystalline and noncrystalline (amorphous) regions. The aromatic, carboxyl and aliphatic molecular groups are nearly planar in configuration and exist in a side-by-side arrangement. Stabilization distances between atoms in neighboring molecules are usually van der Waals contact distances, and there is no structural evidence of any abnormally strong forces among the molecules. The unusually high melting point of PET (compared to aliphatic polyesters) is not the result of any unusual intermolecular forces, but is attributed to ester linkages. The cohesion of PET chains is a result of hydrogen bonds and van der Waals interactions, caused by dipole interaction, induction and dispersion forces among the chains. The capacity to form useful fibers and the tendency to crystallize depend on these forces of attraction. The interactive forces create inflexible tight packing among macromolecules, showing high modulus, strength, and resistance to moisture, dyestuffs and solvents. The limited flexibility in the macromolecule is mainly due to the ethylene group. The extended quenched fiber does not show any early development of crystallinity; the growth of crystals starts to occur upon drawing. A number of basic structural models are required to represent the different states of the fiber: amorphous (no orientation) after extrusion, amorphous (no orientation) after cold drawing, crystalline orientation after thermal treatment and after hot drawing, stretching and annealing. The crystalline oriented form can also be obtained by high stress (high-speed) spinning. Differential Scanning Calorimerty (DSC) can measure crystallinity and molecular orientation within the fibers. This type of analysis is based on distinctly different values of the heats of fusion for crystalline and noncrystalline forms of the polymer. The heat of fusion of the sample is compared with a calibration standard. The crystallinity is determined by the following relationship
Where) Hf is the heat of fusion of a 100% crystalline polymer, reported in the literature to be about 33.45 cal/g (equal to 140 J/g) [4]. The Tg (glass transition temperature) and Tm (melting point) of the fibers can also be determined by DSC analysis. The results of the density and DSC measurements are shown in Table 1.
Table 1: Crystallinity of Polyester Fiber
| Density Gradient | DSC Measurements |
Fiber Type Base Fibers | Density (g/cc) | Crystallinity (%) | Tg (oC) | Tm(oC) | ∆H (Cal/g) | Crystallinity (%) |
A | 1.3803 | 41.22 | 154.3 | 251.3 | 17.19 | 51.38 |
B | 1.3584 | 45.80 | 161.7 | 254.6 | 16.61 | 49.65 |
C | 1.3809 | 41.73 | 152.9 | 255.8 | 15.29 | 45.73 |
D | 1.3871 | 47.34 | 161.0 | 255.5 | 15.40 | 46.03 |
E | 1.3825 | 43.71 | 175.9 | 257.4 | 16.41 | 49.05 |
Tg - Glass transition temperature. Tm - Melting temperature. ∆H - heat of fusion. For more details on Crystallinity refer: Crystallinity The rapid quenched PET without drawing is amorphous. The temperature range of crystallization for PET is From 10oC below the melting point to the temperature a little higher than the glass transition temperature, 250-100oC. Typical PET has 50% crystallinity. The repeat unit of PET is 1.075 nm and is slightly shorter than the length of a fully extended chain (1.09 nm). Therefore, the chains are nearly planar. The crystal unit cell is triclinic with dimensions a = 0.456nm, b = 0.594nm, c = 1.075nm, (= 98.5o, ß = 118o and (= 112o. [11] PET crystal structure is illustrated in Fig. 3. Another factor for crystallization is the position of the benzene rings. If benzene rings are placed on the chain axis (c), then close packing of the molecular chains eases polymer crystallization. 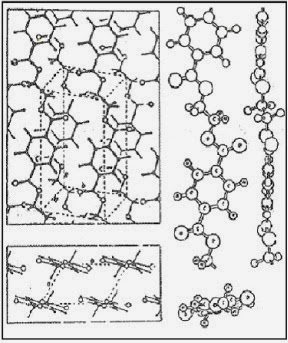 |
Fig 3.Crystal Structure of PET. |
General Polyester Fiber Characteristics: - Strong
- Resistant to stretching and shrinking
- Resistant to most chemicals
- Quick drying
- Crisp and resilient
- Wrinkle resistant
- Mildew resistant
- Abrasion resistant
- Retains heat-set pleats and crease
- Easily washed
MELT-BLOWN PROCESS OF POLYESTER: The IV (intrinsic viscosity) and crystallinity levels of a melt-blown polyester determine the performance of the finished product. A higher IV leads to an increased level of crystallinity, which improves the barrier properties of the polyester melt-blown structure. However, it significantly reduces modulus, toughness and elongation. The advantage of using polyester over such polymers as polyolefins is its heat resistance and greater chemical resistance. Polyesters also offer a moderate oxygen barrier. RELATIONSHIP BETWEEN STRUCTURE, PROPERTIES AND PROCESSING PARAMETERS OF PET FIBERS:
Properties of polyester fibers are strongly affected by fiber structure. The fiber structure, which has a strong influence on the applicability of the fiber, depends heavily on the process parameters of fiber formation such as spinning speed (threadlike stress), hot drawing (stretching), stress relaxation and heat setting (stabilization) speed. As the stress in the spinning threadlike is increased by higher wind-up speed, the PET molecules are extended, resulting in better as-spun uniformity, lower elongation and higher strength, greater orientation and high crystallinity. Hot drawing accomplishes the same effect and allows even higher degrees of orientation and crystallinity. Relaxation is the releasing of strains and stresses of the extended molecules, which results in reduced shrinkage in drawn fibers. Heat stabilization is the treatment to “set” the molecular structure, enabling the fibers to resist further dimensional changes. Final fiber structure depends considerably on the temperature, rate of stretching; draw ratio (degree of stretch), relaxation ratio and heat setting condition. The crystalline and noncrystalline orientation and the percentage of crystallinity can be adjusted significantly in response to these process parameters. Mechanical Properties: As the degree of fiber stretch is increased (yielding higher crystallinity and molecular orientation), so are properties such as tensile strength and initial Young’s modulus. At the same time, ultimate extensibility, i.e., elongation is usually reduced. An increase of molecular weight further increases the tensile properties, modulus, and elongation. Typical physical and mechanical properties of PET fibers are given in Table 2. And stress-strain curves in Fig. 4. It can be seen that the filament represented by curve C has a much higher initial modulus than the regular tenacity staple shown in curve D. On the other hand, the latter exhibits a greater tenacity and elongation. High tenacity filament and staple (curve A and B) have very high breaking strengths and moduli, but relatively low elongations. Partially oriented yarn (POY) and spun filament yarns, exhibit low strength but very high elongation (curve E). When exposing PET fiber to repeated compression (for example, repeated bending), so-called kink bands start to form, finally resulting in breakage of the kink band into a crack. It has been shown in [5] that the compressibility stability of PET is superior to that of nylons. Table 2: Physical Properties of Polyester Fibers
| Filament yarn | Staple and tow
|
Property | Regular tenacitya | High tenacityb | Regular tenacityc | High tenacityd |
breaking tenacity,e N/tex | 0.35-0.5 | 0.62-0.85 | 0.35-0.47 | 0.48-0.61 |
breaking elongation | 24-50 | 10-20 | 35-60 | 17-40 |
elastic recovery at 5% elongation, % | 88-93 | 90 | 75-85 | 75-85 |
initial modulus, N/texf | 6.6-8.8 | 10.2-10.6 | 2.2-3.5 | 4.0-4.9 |
specific gravity | 1.38 | 1.39 | 1.38 | 1.38 |
Moisture regian, % | 0.4 | 0.4 | 0.4 | 0.4 |
Melting temperature, oC | 258-263 | 258-263 | 258-263 | 258-263 |
a-Textile-filament yarns for woven and knit fabrics.b-Tire cord and high strength, high modulus industrial yarns. c-Regular staple for 100% polyester fabrics, carpet yarn, fiberfill, and blends with cellulosic blends or wool. d-High strength, high modulus staple for industrial applications, sewing thread, and cellulosic blends. e-Standard measurements are conducted in air at 65% rh and 22oC.fTo convert N/text to ge/den, multiply by 11.33.gThe equilibrim moisure content of the fibers at 21oC and 65% rh. 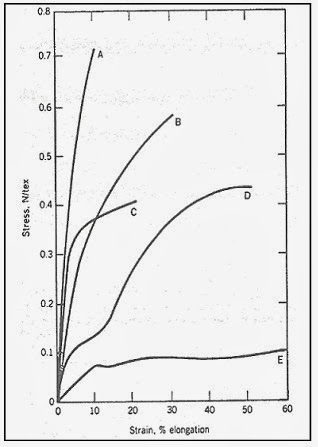 |
Fig 4. Typical stress strain curve for PET fibers.(A-High tenacity filament,B-High tenacity staple, C-regular tenacity filament,D-regular tenacity staple,C-POY filament) |
Shrinkage varies with the mode of treatment. If relaxation of stress and strain in the oriented fiber is allowed to occur through shrinkage during fiber manufacture, then shrinkage at the textile processing stage is reduced and initial modulus is lowered. Polyester yarns held to a fixed length under tension during heat treatment are less affected with change in modulus, and reduced shrinkage values can still be obtained. This is very important in fiber stabilization. PET shows nonlinear and time-dependent elastic behavior. It recovers well from stretch, compression, bending, and shear because of its relatively high initial modulus. Extensional creep occurs under load, with subsequent delay in recovery upon removal of the load. But compared with other melt-spun fibers, the creep is small. The formation of small fuzz balls of entangled fibers (pills) on the fabric surface can be a serious problem. Fuzz formation may be affected by friction, stiffness, breaking strength and abrasion resistance. Shape, fineness, stiffness, recovery, friction and elongation influence entanglement of fibers. After the pills have been formed, their rate of wear-off can affect the fabric appearance. Wear-off is a function of fiber breaking strength and flex life. Reducing the molecular weight, which affects the abrasion resistance; flex life, and breaking strength, results in a decrease in pilling tendency of PET fiber. However, spinning low molecular weight linear PET fiber is difficult. As the molecular weight is reduced, the melt viscosity decreases and a uniform fiber with satisfactory continuity of spinning cannot be produced. Melt viscosity can be raised by the addition of a cross-linking compound, which is prone to hydroxyl groups. Another property, important especially to the apparel industry, is crimp stability or crimp compression. Generally, the tighter the packing of molecular chains, the stiffer and more mechanically resistant the fiber is. Crimp stability of the fiber can be improved with an increase in heating temperature. In addition, crimp compression of the fiber can be decreased by increasing draw ratio when the fiber is produced. Chemical Properties: Polyester fibers have good resistance to weak mineral acids, even at boiling temperature, and to most strong acids at room temperature, but are dissolved with partial decomposition by concentrated sulfuric acid. Hydrolysis is highly dependent on temperature. Thus conventional PET fibers soaked in water at 70oC for several weeks do not show a measurable loss in strength, but after one week at 100oC, the strength is reduced by approximately 20%. Polyesters are highly sensitive to bases such as sodium hydroxide and methylamine, which serve as catalysts in the hydrolysis reaction. Methylamine penetrates the structure initially through noncrystalline regions, causing the degradation of the ester linkages and, thereby, loss in physical properties. This susceptibility to alkaline attack is sometimes used to modify the fabric aesthetics during the finishing process. The porous structures produced on the fiber surface by this technique contribute to higher wettability and better wear properties [7]. Polyester displays excellent resistance to oxidizing agents, such as conventional textile bleaches, and is resistant to cleaning solvents and surfactants. Also, PET is insoluble in most solvents except for some polyhalogenated acetic acids and phenols. Concentrated solutions of benzoic acid and o-phenylphenol have a swelling effect. PET is both hydrophobic and oleophilic. The hydrophobic nature imparts water repellency and rapid drying. But because of the oleophilic property, removal of oil stains is difficult. Under normal conditions, polyester fibers have a low moisture regain of around 0.4%, which contributes to good electrical insulating properties even at high temperatures. The tensile properties of the wet fiber are similar to those of dry fiber. The low moisture content, however, can lead to static problems that affect fabric processing and soiling. Optical Properties: PET has optical characteristics of many thermoplastics, providing bright, shiny effects desirable for some end uses, such as silk-like apparel. Recently developed polyester microfiber with a linear density of less than 1.0 denier per filament (dpf), achieves the feel and luster of natural silk. Thermal Properties: The thermal properties of PET fibers depend on the method of manufacture. The DTA (Fig. 5.) and TMA (Fig. 6) data for fibers spun at different speeds show peaks corresponding to glass transition, crystallization, and melting regions. Their contours depend on the amorphous and crystalline content. The curves shown for 600 m/min and above are characteristic of drawn fiber. The glass transition range is usually in the range of 75oC; crystallization and melting ranges are around 130oC and 260oC, respectively. 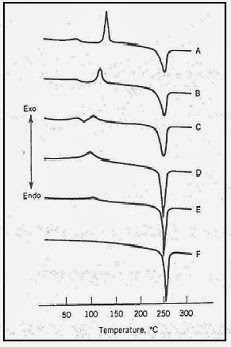 |
Fig 5.TDA curves of PET yarns spun at different spinning speeds [m/min], A-2000, B-3000,C-4000,D-4500,E-5000,F-6000. |
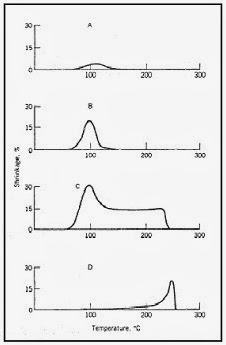 |
Fig 6.TMA curve (shrinkage) of spun yarn at different spinning speeds[m/mn] A-less than 1000,B-1000-2000, C-2000-5000, D- greater than 6000. |
The thermal degradation of PET proceeds by a molecular mechanism with random chain scission at ester linkages, although a radical mechanism has also been proposed. A chain-scission scheme is shown below: The degradation products can undergo further changes, but at ordinary processing temperatures a certain proportion of carboxyl groups is introduced into the polymer structure. Color formation upon degradation has been attributed to the formation of polyenaldehydes from acetaldehyde and from a further breakdown of poly(vinyl ester)s. DYEING PROPERTIES: Because of its rigid structure, well-developed crystallinity and lack of reactive dyesites, PET absorbs very little dye in conventional dye systems. This is particularly true for the highly crystalline (highly drawn), high tenacity-high modulus fibers. Polyester fibers are therefore dyed almost exclusively with disperse dyes. A considerable amount of research work has been done to improve the dyeability of PET fibers. Polymerizing a third monomer, such as dimethyl ester, has successfully produced a cationic dyeable polyester fiber into the macro-molecular chain. This third monomer has introduced functional groups as the sites to which the cationic dyes can be attached [8]. The third monomer also contributes to disturbing the regularity of PET polymer chains, so as to make the structure of cationic dyeable polyester less compact than that of normal PET fibers. The disturbed structure is good for the penetration of dyes into the fiber. The disadvantage of adding a third monomer is the decrease of the tensile strength. A new dyeing process for polyester fiber at low temperature (40(C and below) has been reported [9]. This method employs a disperse dye in a microemulsion of a small proportion of alkyl halogen and phosphoglyceride. The main advantage of this method is low temperature processing, but there remains the environmental problem that is produced by using toxic carriers. Another approach has been introduced by Saus et al [20]. The textile industry uses large amounts of water in dyeing processes emitting organic compounds into the environment. Due to this problem a dying process for polyester fiber was developed, in which supercritical CO2 is used as a transfer medium [21]. This gives an option avoiding water discharge. It is low in cost, non-toxic, non-flammable and recyclable. When dyed in an aqueous medium, reduction clearing is to be carried out to stabilize color intensity, which produces more wastewater. Reduction clearing is not carried out following supercritical dyeing. Other advantages are better control of the dying process and better quality of application achieved. Spun bond PET nonwoven webs have been treated by (SO2+O2) plasma and (N2+H2+He) plasma at the University of Tennessee, Knoxville. The research results show that spun bond PET nonwovens web can be colored by conventional water-soluble acid dyes [10]. Plasma techniques open new avenues for coloring PET fabrics and are sure to be more evident in the coloring of polyester fibers in the future. SPIN FINISH PROPERTIES: Several types of spin finishes are available. There are only few spin finish manufacturers - Takemoto, Matsumoto, Kao from Japan, Henkel, Schill &Scheilacher, Zimmer & Schwarz and Hoechst from Germany and George A.Goulston from USA. It is only by a mill trial that the effectiveness of a spin finish can be established.A spin finish is supposed to give high fibre to fibre friction of 0.4 to 0.45, so as to control fibre movement particularly at selvedges , low fibre-metal friction of 0.2 to 0.15 to enable lower tensions in ring spinning and provide adequate static protection at whatever speed the textile machine are running and provide enough cohesion to control fly and lapping tendencies and lubrication to enable smoother drafting.Spin finish as used normally consists of 2 components - one that gives lubrication / cohesion and other that gives static protection. Each of these components have upto 18 different components to give desired properties plus anti fungus, antibacterial anti foaming and stabilisers.Most fibre producers offer 2 levels of spin finishes. Lower level finish for cotton blends and 100% polyester processing and the higher level finish for viscose blend. The reason being that viscose has a tendecy to rob polyester of its finish. However in most of the mills even lower spin finish works better for low production levels and if the production level is high, high level spin finish is required if it is mixed with viscose.For OE spinning where rotor speeds are around 55000 to 60000 rpm standard spin finish is ok, but if a mill has new OE spinning machines having rotors running @80000 rpm, then a totally different spin finish which has a significantly lower fibre - fibre and fibre - metal friction gave very good results. The need to clean rotors was extended from 8 hours to 24 hours and breaks dropped to 1/3rd.In conclusion it must be stated that though the amount of spin finish on the fibre is only in the range 0.105 to 0.160, it decides the fate of the fibre as the runnability of the fibre is controlled by spin finish, so it is the most important component of the fiber Effectiveness of spin finish is not easy to measure in a fibre plant. Dupont uses an instrument to measure static behaviour and measures Log R which gives a good idea of static cover. Also, there is s Japanese instrument Honest Staticmeter, where a bundle of well conditioned fibre is rotated at high speed in a static field of 10000 volts. The instrument measures the charge picked up by the fibre sample, when the charge reaches its maximum value, same is recorded and machine switched off. Then the time required for the charge to leak to half of its maximum value is noted. In general with this instrument , for fibre to work well, maximum charge should be around 2000 volts and half life decay time less than 40 sec. If the maximum charge of 5000 and half life decay time of 3 min is used , it would be difficult to card the fibre , especially on a high production card. Polyester Properties - Dry Heat ShrinkageNormally measured at 180 degree C for 30 min. Values range from 5 to 8 %. With DHS around 5%, finished fabric realisation will be around 97% of grey fabric fed and with DHS around 8% this value goes down to 95%. Therefore it makes commercial sense to hold DHS around 5%.L and B colourL colour for most fibres record values between 88 to 92. “b” colour is a measure of yellowness/blueness. b colour for semidull fibre fluctuates between 1 to 2.8 with different fibre producers. Lower the value, less is the chemicals degradation of the polymer. Optically brightened fibres give b colour values around 3 to 3.5. This with 180 ppm of optical brightner.Dye Take UpEach fibre producer has limits of 100 +- 3 to 100+-8. Even with 100+-3 dye limits streaks do occur in knitted fabrics. The only remedy is to blend bales from different days in a despatch and insist on spinning mills taking bales from more than one truck load.Fused FibersThe right way to measure is to card 10 kgs of fibre. Collect all the flat strips(95% of fused fibres get collected in flat strips). Spread it out on a dark plush, pick up fused and undrawn fibres and weigh them. The upper acceptable limit is 30mgm /10kgs. The ideal limit should be around 15mgm/10kgs. DUpont calls fused/undrawn fibres as DDD or Deep Dyeing Defect.Polyester LustrePolyester fibres are available in Bright : 0.05 to 0.10 % TiO2 Semil dull : 0.2 to 0.3 % TiO2 Dull : 0.5 % TiO2 Extra dull : 0.7% TiO2 and in optically brightened with normally 180 ppm of OB, OB is available in reddish , greenish and bluish shades. Semi dull is the most popular lustre followed by OB (100 % in USA) and bright. CUT- LENGTH PROPERTIES: Cut lengths available are 32, 38, 44, 51 and 64mm for cotton type spinning and a blend of 76, 88 and 102 mm - average cut length of 88m for worsted spinning. The most common cut length is 38 mm.
For blending with other manmade fibres, spinners preferred 51mm to get higher productivity, because T.M. will be as low as 2.7 to 2.8 as against 3.4 to 3.5 for 38mm fibre. If the fibre legnth is more, the nepping tendency is also more , so a crompromise cutlength is 44 mm. With this cut length the T.M. will be around 2.9 to 3.0 and yarns with 35 to 40% lower imprfections can be achieved compared a to similar yarn with 51 mm fibre. In the future spinners will standardise for 38 mm fibre when the ringspinning speed reaches 25000 rpm for synthetic yarns.
For OE spinning , 32 mm fibre is preferred as it enables smaller dia rotor(of 38mm) to be used which can be run at 80000 to 100000 rpm.
Air jet system uses 38 mm fibre.
TENSILE PROPERTIES:
Polyester fibers are available in 4 tenacity levels. Low pill fibres- usuall in 2.0 / 3.0 D for suiting enduse with tenacities of 3.0 to 3.5 gpd(grams per denier). These fibres are generally used on worsted system and 1.4D for knitting Medium Tenacity - 4.8 to 5.0 gpd- High Tenacity - 6.0 to 6.4 gpd range and
- Super high tenacity - 7.0 gpd and above
Both medium and high tenacity fibres are used for apparel enduse. Currently most fibre producers offer only high tenacity fibres. Spinners prefer them since their use enables ring frames to run at high speeds, but then the dyeablity of these fibres is 20 to 25% poorer, also have lower yield on wet processing, have tendency to form pills and generally give harsher feel. The super high tenacity fibres are used essentially for spinning 100% polyester sewing threads and other industrial yarns. The higher tenacities are obtained by using higher draw ratios and higher annealer temperatures upto 225 to 230 degree C and a slight additional pull of 2% or so at the last zone in annealing. Elongation is inversely proportional to tenacity e.g ————- Tenacity——-Elongation at Break———T10 Values Low Pill——3.0-3.5————45-55%——————————1.0-1.5 Medium——4.8-5.0————25-30%——————————3.5-4.0 High————6.0-6.4————16-20%——————————5.2-5.5 Super Hi——7.0 plus———-12-14%——————————6.0 plus The T10 or tenacity @ 10% elongation is important in blend spinning and is directly related to blend yarn strength. While spinning 100% polyester yarns it has no significance. Tenacity at break is the deciding factor.Other Properties: Polyester fibers display good resistance to sunlight but long-term degradation appears to be initiated by ultraviolet radiation. However, if protected from daylight by glass, PET fiber gives excellent performance, when enhanced by an UV stabilizer, in curtains and automobile interiors. Although PET is flammable, the fabric usually melts and drops away instead of spreading the flame. PET fiber will burn, however, in blends with cotton, which supports combustion. Polyester has good oxidative and thermal resistance. Color forming species are produced and carboxyl end groups are increased. The resistance to both oxidative and thermal degradation may be improved by antioxidants. Mechanical properties are not affected by moderate doses of high-energy radiation. At doses of more than 0.5Mgy (Mrad), the tensile strength and ultimate elongation decrease, and deteriorate rapidly at 1-5 Mgy (100-500Mrad). Finally the resistance of polyester fibers to mildew, aging and abrasion is excellent. Molds, mildew and fungus may grow on some of the lubricants or finishes, but do not attack the fiber. APPLICATIONS: DuPont Company produced the first U.S. commercial polyester fiber in 1953. Since polyester fiber has a lot of special characteristics, most of them are used in the following three major areas: - Apparel: Every form of clothing
- Home Furnishings: Carpets, curtains, draperies, sheets and pillowcases, wall coverings, and upholstery
- Other Uses: Hoses, power belting, ropes and nets, thread, tire cord, auto upholstery, sails, floppy disk liners, and fiberfill for various products including pillows and furniture
Surgeon’s gowns, for example, were once woven linen but are now for the most part repellant treated entangled polyester fiber pulp composites on spun bond melt blown laminates. These new gowns are far superior to the older material in providing a breathable barrier between the surgeon and the patient, which serves to significantly reduce hospital infections. Spun lace mattress pad facing of 100% polyester continues to be the replacement of spun bond material because of the textile-like character of entangled fiber fabrics. PET has become the most important polymer type of fibrous prostheses. It is reasonably inert, biocompatible, flexible, and resilient and has an appropriate level of tissue acceptance. But, polymerization initiators, antioxidants, titanium dioxide and other impurities should be minimized to improve its bio compatibility. Thermoplastics such as polyester are usually considered less flammable than cellulosic fibers because they melt and shrink of drip away from the flame. Polyester resin such as Crystar, a DuPont trade name, is used to produce spun bonded polyester in a variety of applications: a nonwoven sheet fabric, fabric softener dryer sheets filtration media, apparel interlining, carpet backing, furniture and bedding, automotive seats and agricultural crop covers. One of the important applications of PET is in the form of bi-component fibers. To increase the strength of the nonwoven fabric, in while maintaining the soft hand of LLDPE, PET is used in continuous bicomponent filaments having a sheath component made of LLDPE and a core component made of PET. The tensile strength of the fabrics is improved remarkably by the bi-component filaments and depends on the LLDPE/PET ratio. The ultrasonically bonded polyester/polypropylene blend like Matarh’s Ultraskin, the protective clothing, is said to protect wearers from rain while offering the breathability needed to provide comfort. Dry and wet laid nonwovens made from a range of synthetic and inorganic fibers are used in various insulation and industrial applications. A series of nonwoven polyester fiber mats are used in class F (155 c) DMD flexible electrical insulation laminates and electrical tape backing applications. Nonwoven mats made of polyester fibers and high temperature resistant m-Aramid is used as a cost effective replacement for Aramid paper in class H (180 C) flexible electrical insulation composites. [28] Composites made of 100% polyester fibers are widely used as filtration media. Its layered structure gives excellent tear strength, a smooth, fiber free surface and edge stability. These products provide higher filtration efficiencies than spun bonded media that has not been calendared. The main advantage of these products is that they have no short fibers to be carried downstream and contaminate the filtrate. In Fiberfill applications polyester fibers are used inside seat cushions, back pillows, mattresses and waterbeds, decorative and throw pillows, outdoors furniture and even hand-stuffed custom upholstery. REFERENCES - Froehlich, Fritz W.: “Restructuring, Innovation See Akzo Nobel Through Difficult Business Environment “, International Fiber Journal, (12), 3, 1997
- Harrison, David: “Synthetic Fibers for Nonwovens Update” Nonwovens Industry, 28 (6) 32- 39 (1997)
- Hearle, J.W.S., Miraftab, M.: “The Flex Fatigue of Polyamide and Polyester Fibers. Part II : The Development of Damage Under Standard Conditions” Journal of Materials Science 30(4) 1661-70 (1995)
- V.B. Gupta and V.K. Kothari, “ Manufactured fiber Technology”
- http://textilelearner.blogspot.com/2013/08/an-overview-of-polyester-fiber.html