Finishing Processes of Textile
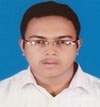
Saik Al Maruf
Dept. of Textile Engineering
Specialized in Dyeing, Printing & Finishing
Ahsanullah University of Science and Technology
Email: saikalmaruf40@gmail.com
Introduction After construction of fabric through one of the many techniques described above, it is known as greige good or gray good. This simply denotes any unfinished fabric. Many finishing processes are employed for improving the appearance, feel and durability of the fabric. These processes are broadly classified as Preparatory Processes, Stabilizing Processes, and Textural Processes.
Preparatory Processes
The unfinished fabric or the gray good may contain many impurities such as dirt, soil, sizing, oils and other additives. As such, they need to be cleaned before proceeding towards finishing of the textile.
Singeing or Gassing
In this process one or both sides of a fabric are passes rapidly over a gas flame to burn off the protruding fibers. For thermoplastic fibers other methods including infra-red or heat is used. Thermoplastic fibers are harder to singe as compared to cotton or other such fibers because they melt and form hard residues on the fabric surface. When singeing is done in the yarn stage, it is called gassing.
Bleaching
It is the process of decolorization for removing all natural colors from the gray good. It is a chemical based process. Bleaching is further classified into oxidative bleaching and reductive bleaching. Natural fibres are all generally bleached with oxidative methods using such chemicals as sodium hypochlorite, sodium chlorite or hydrogen peroxide. Fibers like Polyamide, Polyacrylics and Polyacetates are generally bleached using reductive bleaching technology using sodium hydrosulphite, a powerful reducing agent. In addition to bleaching, Optical Brightening Agents (OBA) are also applied to give the textile material a brilliant white look.
Stabilizing Processes
Stabilizing processes are required for improving properties such as strength, luster, and other qualities of the fiber.
Mercerization
This process is important for cotton fabric which is treated with a caustic solution for improving properties such as fiber strength, shrinkage resistance, luster, and dye affinity. The yarn or fiber is dipped in a solution of sodium hydroxide and then treated with water or acid to neutralize the sodium hydroxide. A variation of this process is hot mercerization. It adds more value to the fabric. This process involves saturation of fabric in caustic soda solution at higher temperatures and then cooling, stretching and final washing.
Ammoniating
It is done for increasing luster, affinity for dyes, abrasion resistance, smoothness etc. particularly of cotton and rayon fabrics. The yarn or fabric is passed through a weak solution of ammonium at such temperatures at which swelling and shrinkage occur. Then it is rapidly passed through hot water and dried in hot air.
Shrinking
The fibers have tendency of reverting back to their natural state, thus causing shrinkage of the fabric. To avoid the subsequent shrinkage, the process of shrinking the gray good is carried out through different methods such as immersion in cold water, followed by hot water, steaming, resin or a chemical treatment.
Tentering
He main purpose of tentering is drying and making the fabric even for further processing. The tenter frames consist of two endless chains having an adjustable distance within them. The fabric runs through this frame and is carried into the heated housing where a blast of hot air removes any moisture present in the fabric.
Decating
Improves luster, appearance, feel as well as preshrinks the fabric. It may be applied to woven as well as knitted fabrics. Wet decating and dry decating are the two methods adopted. Wet decating is generally used for woollen fabrics. The fabric is wound on a perforated roller and treated in hot water or steam boiler. In dry decating, the fabric is passed together with a blanket around a perforated cylinder. The moist heat causes the fibers to become wrinkle free.
Enzyme Washing
Sometimes enzymes are used to produce stone washed effects on fabrics. Enzymes are organic catalysts that are used for speeding up a chemical reaction. This process is less damaging to fabrics than actual stone washing. Also, it gives a very soft feel to the treated fabric
Textural Processes
Textural processes are meant for improving the texture of the fabric such as stiffness, smoothness, weight or strength.
Temporary Stiffening Fabrics, particularly cotton and linen, are given a temporary stability and stiffness by application of a firming agent which is often a solution of starch. It is commonly known as ‘starching’ or ‘temporary stiffening’. When this process is done while preparing warp for weaving, it is called ‘sizing’ and ‘dressing’. The term ‘dressing’ is generally used for the warp of wool. Other than starch, the substances used for stiffening fabrics are flour, dextrine, glue, shellac, fats, wax, and paraffin. Sometimes clay, chalk, barium sulfate, calcium sulfate or magnesium sulfate are also used for stiffening cotton fabrics. At times back starching is also done in which only the back side of the fabric is starched. Temporary stiffening is required to retain the freshness of the fabric till it is not used for making any product. Stiffening also allows the fabric to be cut more easily into patterns for the textile products.
Permanent Stiffening The fabrics which are permanently stiffened usually need less laundering and therefore become more durable. Permanent Stiffening is done by chemical processes that change the cellular structure of the fiber. This process makes the fabric smoother and dirt resistant as the dirt tends to slide off rather than cling onto the fabric. Some of the permanent finishes are Ankord, Basco, Clearight, Kandarized, Saylerizing, Sheercroft, Staze- Right and Turbenizing. They all give the fabric such properties as tensile strength, luster, shrinkage resistance, crispness, abrasion resistance and improve the appearance of the fabrics. Turbenizing is done to avoid the need of starching fabric for its life. This can be done through three methods. The parts to be stiffened like collar, cuffs, belts are interlined with a thermoplastic fiber or with cellulose acetate or the fabric my be coated with synthetic resin. The thermoplastic fibers melt and bonds with the garment when pressed with a hot iron producing a stiffened fabric. When cellulose acetate is used, it is softened by acetone which is also heat pressed on to the fabric giving permanent stiffness. A coating of resin is also heat pressed on to the fabric.
Weighting
Sometimes the weight of certain fabrics, such as silk, is increased to improve its feel and draping quality by immersing it in a solution having metallic salts. Low-grade wool fabrics are also weighted sometimes by felting short wool fibers into the fabric. These fibers, called flocks, are obtained by washing, brushing and sheering the wool fabrics. Excessive weighting tends to weaken the fabric.
Calendering
Calendering is done to add luster to fabrics. Calenders are heavy machines made up of at least two rollers that can go upto seven in number. Alternately, one roller is made of steel and the other is made of softer material like wool paper, cotton fiber and corn husks. The steel rolls may be equipped to be heated by gas or steam. The fabric passes rapidly between the rolls and then wound up on the back of the machine.
GlazingThe Glazing process consists of treating the fabric with glue, starch, paraffin, shellac, or resin and then moving it through hot friction rollers. This process gives the fabric qualities such as luster, resistance to dust, spots and shrinkage.
EmbossingThrough embossing, raised figures or designs are produced on the surface of the fabrics. This is done by passing the fabric between heated engraved rollers. This process can be applied to all the fabrics except wool. When the process is combined with certain chemical resins, the embossing becomes permanent.
Moireing
Moireing is done through ridged rollers that produce a waved or watered effect on a textile fabric. The design becomes permanent when heat-set. A moire pattern obtained on a rayon fabric is not permanent. On silk, it comparatively remains for a longer time but diminishes gradually. Moireing is permanent on acetate, nylon or other thermoplastic fibers because these fabrics have the tendency to melt when subjected to heat. When cooled down, the pattern is conformed and hardened on the fabric.
BeetlingBeetling process is applied to linen or cotton. The fabric is beaten with large wooden blocks in order to produce a hard, flat surface with a sheen. Only table linen is put through beetling and not the dress linen. When applied to cotton fabrics, beetling gives it the feel and appearance of linen. This process permanently flattens the yarns of the fabric on which it is applied.
Raising For giving a hairy surface to a fabric, several methods are adopted for pulling fiber ends to its surface. This fabric is then known as raised fabric. It is different from pile construction ( such as tufting) which is woven or knitted with extra yarns placed on the fabric. Some of the methods of raising are Napping, Sanding, Gigging and Tigering.
Napping
It is done to get a deep hairy surface. The fabric is passed under a roller having fine steel wires with small hooks on the ends. The hooks scrape the surface of the fabric pulling up the fiber ends. It produces a soft fabric with air trapped in the cells lending warmth to the fabric. Flannellete and wool flannel are the examples of napped fabrics. When both sides of a fabric are napped in one direction, it is called single napping. When both surfaces are napped in opposite directions, it is called double napping.
Sanding When a fabric is passed through a series of emery-covered rollers, it gets a suedelike surface. This is known as sanding or emerizing. A soft nap is produced by this process.
Gigging
This raising process is applied to wool fabrics. The raised fibers of wet fabric are brushed in one direction which gives a smooth and lustrous appearance to the fabric.
TigeringA tigering finish is given to a fabric already having naps. This improves the height of the raised naps and removes the loose fibers. The tiger roll, with long fine wires, pulls up the fibers that are not raised by the process of napping. This process is generally applied to such fabrics as velour, plush and imitation fur.
Shearing
Shearing refers to the process of trimming the pile on a fabric to a desired height. This process gives an attractive and smooth surface to the fabric. Patterns can also be made by shearing through high and low surface levels. It is done by a machine having rotating cylinders with spiral blades. Its action resembles that of a lawn mower.
Crepe and Crinkled Effects Some of the finishing processes impart crepe or crinkled effects to the fabric. This is done through various methods. One method involves the use of engraved rollers. In another method, cotton is treated with caustic soda which is applied in the form of stripes and then the fabric is washed. The portions having soda shrinks and the remaining parts gather into small wrinkles. In yet another method, wax is used in place of caustic soda. Silk is sometimes given a crepe effect by carefully applying sulfuric acid to it.
Finishing Processes for Functionality of Fibers
The finishing processes that have been described in the above section improve the appearance and feel of the treated fabric. There are other finishing processes that give special properties to the fabric for particular functions.
Water Repellency The fabrics that do not allow absorption or penetration of water for a fixed period of time are said to be water-repellent fabrics. As opposed to waterproof fabrics, these fabrics are porous for allowing body perspiration to escape and therefore are more comfortable. Some fibers such as nylon and polyester do not readily absorb water where as other fibers such as cotton and rayon can absorb water easily. Therefore, often the fibers of water absorbent fabrics are preferred for making items such as rain coats. As the time of water resistance differ, the garments too differ in their properties. The shower-resistant garments are effective for light rains only and rain-resistant garments for moderate rains where as storm-resistant garments can resist water penetration for many hours and are suitable for heavy rains.
There are generally three types of finishes given to water repellent fabrics. These are nondurable, semidurable and durable finishes.
Nondurable Finishes
These finishes are based upon a paraffin wax-aluminum acetate emulsion. This emulsion is applied through padding and drying operations. Sometimes zirconium salts are used instead of aluminum which gives better water repellency. These fabrics loose water repellency if subjected to heavy washing or dry cleaning.
Semidurable Finishes
Wax and salt solutions are used for these types of finishes. However, they can not stand laundering but are resistant to dry cleaning.
Durable Finishes
There are many approaches for producing flame retardant fabrics such as application of chemical finishes, manufacturing of modified manmade fibers or new flame retardant fibers. The chemicals mostly used for giving flame retardant finishes include ammonia?cured tetrakis-hydroxymethyl-phosphonium hydroxide (THPOH), decabromodiphenyloxide (DBDPO), halogen phosphorous, nitrogen phosphorous, boron phosphorous, inorganic salts and others. Sometimes, flame retardant fibers are created by adding certain chemicals to existing solutions for making fibers. They are more stable and safer for human health. Special flame retardant fibers are also developed which are more flame resistant than the other two types.
Flame Retardants Wax and salt solutions are used for these types of finishes. However, they can not stand laundering but are resistant to dry cleaning.
Slip Resistance
Other than rough surfaced fabrics with hard twisted yarns, some fabrics have the tendency of slipping. Permanent firmness is given to such fabrics by immersing them in synthetic resins, then stretching and drying them under tension.
Calendering
Calendering is done to add luster to fabrics. Calenders are heavy machines made up of at least two rollers that can go upto seven in number. Alternately, one roller is made of steel and the other is made of softer material like wool paper, cotton fiber and corn husks. The steel rolls may be equipped to be heated by gas or steam. The fabric passes rapidly between the rolls and then wound up on the back of the machine.
GlazingThe Glazing process consists of treating the fabric with glue, starch, paraffin, shellac, or resin and then moving it through hot friction rollers. This process gives the fabric qualities such as luster, resistance to dust, spots and shrinkage.
EmbossingThrough embossing, raised figures or designs are produced on the surface of the fabrics. This is done by passing the fabric between heated engraved rollers. This process can be applied to all the fabrics except wool. When the process is combined with certain chemical resins, the embossing becomes permanent.
Moireing
Moireing is done through ridged rollers that produce a waved or watered effect on a textile fabric. The design becomes permanent when heat-set. A moire pattern obtained on a rayon fabric is not permanent. On silk, it comparatively remains for a longer time but diminishes gradually. Moireing is permanent on acetate, nylon or other thermoplastic fibers because these fabrics have the tendency to melt when subjected to heat. When cooled down, the pattern is conformed and hardened on the fabric.
BeetlingBeetling process is applied to linen or cotton. The fabric is beaten with large wooden blocks in order to produce a hard, flat surface with a sheen. Only table linen is put through beetling and not the dress linen. When applied to cotton fabrics, beetling gives it the feel and appearance of linen. This process permanently flattens the yarns of the fabric on which it is applied.
Raising For giving a hairy surface to a fabric, several methods are adopted for pulling fiber ends to its surface. This fabric is then known as raised fabric. It is different from pile construction ( such as tufting) which is woven or knitted with extra yarns placed on the fabric. Some of the methods of raising are Napping, Sanding, Gigging and Tigering.
Napping
It is done to get a deep hairy surface. The fabric is passed under a roller having fine steel wires with small hooks on the ends. The hooks scrape the surface of the fabric pulling up the fiber ends. It produces a soft fabric with air trapped in the cells lending warmth to the fabric. Flannellete and wool flannel are the examples of napped fabrics. When both sides of a fabric are napped in one direction, it is called single napping. When both surfaces are napped in opposite directions, it is called double napping.
Sanding When a fabric is passed through a series of emery-covered rollers, it gets a suedelike surface. This is known as sanding or emerizing. A soft nap is produced by this process.
Gigging
This raising process is applied to wool fabrics. The raised fibers of wet fabric are brushed in one direction which gives a smooth and lustrous appearance to the fabric.
TigeringA tigering finish is given to a fabric already having naps. This improves the height of the raised naps and removes the loose fibers. The tiger roll, with long fine wires, pulls up the fibers that are not raised by the process of napping. This process is generally applied to such fabrics as velour, plush and imitation fur.
Shearing
Shearing refers to the process of trimming the pile on a fabric to a desired height. This process gives an attractive and smooth surface to the fabric. Patterns can also be made by shearing through high and low surface levels. It is done by a machine having rotating cylinders with spiral blades. Its action resembles that of a lawn mower.
Crepe and Crinkled Effects Some of the finishing processes impart crepe or crinkled effects to the fabric. This is done through various methods. One method involves the use of engraved rollers. In another method, cotton is treated with caustic soda which is applied in the form of stripes and then the fabric is washed. The portions having soda shrinks and the remaining parts gather into small wrinkles. In yet another method, wax is used in place of caustic soda. Silk is sometimes given a crepe effect by carefully applying sulfuric acid to it.
Finishing Processes for Functionality of Fibers
The finishing processes that have been described in the above section improve the appearance and feel of the treated fabric. There are other finishing processes that give special properties to the fabric for particular functions.
Water Repellency The fabrics that do not allow absorption or penetration of water for a fixed period of time are said to be water-repellent fabrics. As opposed to waterproof fabrics, these fabrics are porous for allowing body perspiration to escape and therefore are more comfortable. Some fibers such as nylon and polyester do not readily absorb water where as other fibers such as cotton and rayon can absorb water easily. Therefore, often the fibers of water absorbent fabrics are preferred for making items such as rain coats. As the time of water resistance differ, the garments too differ in their properties. The shower-resistant garments are effective for light rains only and rain-resistant garments for moderate rains where as storm-resistant garments can resist water penetration for many hours and are suitable for heavy rains.
There are generally three types of finishes given to water repellent fabrics. These are nondurable, semidurable and durable finishes.
Nondurable Finishes
These finishes are based upon a paraffin wax-aluminum acetate emulsion. This emulsion is applied through padding and drying operations. Sometimes zirconium salts are used instead of aluminum which gives better water repellency. These fabrics loose water repellency if subjected to heavy washing or dry cleaning.
Semidurable Finishes
Wax and salt solutions are used for these types of finishes. However, they can not stand laundering but are resistant to dry cleaning.
Durable Finishes
There are many approaches for producing flame retardant fabrics such as application of chemical finishes, manufacturing of modified manmade fibers or new flame retardant fibers. The chemicals mostly used for giving flame retardant finishes include ammonia?cured tetrakis-hydroxymethyl-phosphonium hydroxide (THPOH), decabromodiphenyloxide (DBDPO), halogen phosphorous, nitrogen phosphorous, boron phosphorous, inorganic salts and others. Sometimes, flame retardant fibers are created by adding certain chemicals to existing solutions for making fibers. They are more stable and safer for human health. Special flame retardant fibers are also developed which are more flame resistant than the other two types.
Flame Retardants Wax and salt solutions are used for these types of finishes. However, they can not stand laundering but are resistant to dry cleaning.
Slip Resistance
Other than rough surfaced fabrics with hard twisted yarns, some fabrics have the tendency of slipping. Permanent firmness is given to such fabrics by immersing them in synthetic resins, then stretching and drying them under tension.
No Responses to "Textile Finishing Processes"