Introduction:
Plated fabrics can be knitted on flat knitting machines. Although there were several issues related to this matter previously, though it’s been over come from those matters nowadays
Knitting effect of weft plating was influenced by the yarn type, the knitting devices and the stitch structure.
The yarn type had a great influence on the plating effect. To obtain an attractive cover effect,
Design of the yarn carrier
The fabric structure was cotton yarn outside, Superfine polypropylene filament inside and Lycra in the middle. According to the conventional plating technique, the laying lengthwise angle and lateral angle of cotton should both be smaller than that of polypropylene, and the lycra should be in the middle. The laying position is shown in Figure 1
There ‘d’ is polypropylene, ‘e’ is lycra and ‘f’ is cotton. According to the new plating concept, the laying lengthwise angle of polypropylene should be greater than that of cotton, the laying lateral angle of polypropylene should be smaller than that of cotton, and that of Lycra should be between those values. The laying position is shown in Figure 1.b. This kind of laying position should ensure the cotton yarn enters the hook first and keeps steady. Then, the polypropylene filament enters the hook along with the closure of the needle latch. This guarantees that the yarn position remains steady, and decreases the misplating problems.
Configuration of the yarn carrier
The configuration of the yarn carrier is as shown in Figure 2. ‘a’ is the guide eye of the ground yarn, ‘b’ is the guide eye of the middle yarn and ‘c’ is the guide eye of the face yarn. The guide eye ‘a’ is fixed, but ‘b’ and ‘c’ can slide in the groove to change the laying lengthwise angle. (The unit is mm.)
Laying position
Laying position is the main factor affecting the plating result. Three laying positions were done here. Table 1 gives the laying lengthwise angles and lateral angles of polypropylene, Lycra and cotton at three laying positions. α refers to the laying lengthwise angle and β refers to the laying lateral angle.
Conclusions
This yarn carrier with three guide eyes can knit three-layer plated fabric and effectively control the misplating problems. The design concept for the new yarn carrier was that the laying lengthwise angle of the ground yarn was greater than that of the face yarn; the laying lateral angle of the ground yarn was smaller than that of the face yarn, and the laying position of the middle yarn was between those values. The feeding tension of the ground yarn was also a little larger than that of the face yarn.
Also we can make fleecy fabric using flat knitting machine because flat knitting machine is a versatile machine which can make any type of knitted fabrics that is producing any kind of fabric possible. But the production rate is the limiting factor.
Knitting effect of weft plating was influenced by the yarn type, the knitting devices and the stitch structure.
The yarn type had a great influence on the plating effect. To obtain an attractive cover effect,
- The face yarn should be thicker than that of the ground yarn.
- Both the face and ground yarns should have a steady loop length
- Diameter of the face yarn to the ground yarn should have the ratio of around 1.4 : 1.
Design of the yarn carrier
The fabric structure was cotton yarn outside, Superfine polypropylene filament inside and Lycra in the middle. According to the conventional plating technique, the laying lengthwise angle and lateral angle of cotton should both be smaller than that of polypropylene, and the lycra should be in the middle. The laying position is shown in Figure 1
There ‘d’ is polypropylene, ‘e’ is lycra and ‘f’ is cotton. According to the new plating concept, the laying lengthwise angle of polypropylene should be greater than that of cotton, the laying lateral angle of polypropylene should be smaller than that of cotton, and that of Lycra should be between those values. The laying position is shown in Figure 1.b. This kind of laying position should ensure the cotton yarn enters the hook first and keeps steady. Then, the polypropylene filament enters the hook along with the closure of the needle latch. This guarantees that the yarn position remains steady, and decreases the misplating problems.
![]() |
Figure 1: Laying position |
The configuration of the yarn carrier is as shown in Figure 2. ‘a’ is the guide eye of the ground yarn, ‘b’ is the guide eye of the middle yarn and ‘c’ is the guide eye of the face yarn. The guide eye ‘a’ is fixed, but ‘b’ and ‘c’ can slide in the groove to change the laying lengthwise angle. (The unit is mm.)
![]() |
Figure 2:Yarn carrier configuration |
Laying position is the main factor affecting the plating result. Three laying positions were done here. Table 1 gives the laying lengthwise angles and lateral angles of polypropylene, Lycra and cotton at three laying positions. α refers to the laying lengthwise angle and β refers to the laying lateral angle.
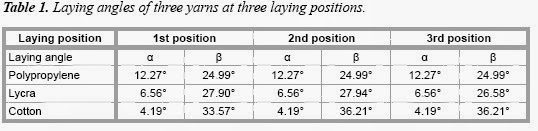
This yarn carrier with three guide eyes can knit three-layer plated fabric and effectively control the misplating problems. The design concept for the new yarn carrier was that the laying lengthwise angle of the ground yarn was greater than that of the face yarn; the laying lateral angle of the ground yarn was smaller than that of the face yarn, and the laying position of the middle yarn was between those values. The feeding tension of the ground yarn was also a little larger than that of the face yarn.
Also we can make fleecy fabric using flat knitting machine because flat knitting machine is a versatile machine which can make any type of knitted fabrics that is producing any kind of fabric possible. But the production rate is the limiting factor.
No Responses to "Analyzing the Possibility of Producing Plated and Fleecy Fabrics onFlat Knitting Machine"