Cotton-The King of Fibers
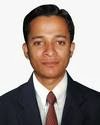
Rahamat Ullah Joy
B.sc in Textile Engineering
Daffodil International University
Email: rahamat.tex@gamil.com
Phone: +8801614445257
History and Origin of Cotton:
Cotton is harvested from almost 32.4 million hectares in more than 40 nations of the temperate and tropic regions of the world (Anonymous, 1981). The crop is grown as far as 470 degrees N latitude in the Ukraine and 370 N latitude in the USA. In the Southern hemisphere production extends to about 320 S latitude (Niles and Feaster, 1984). Cotton grows at an optimum temperature of 300C, where 150C is the minimum temperature for cottonseed germination and growth (Munro, 1987).
![]() |
Cotton |
In the light of increased knowledge of the distribution and relationships of primitive cottons, Santhanam and Hutchinson (1974) reported that the Asiatic species and races probably differentiated before domestication. Fryxell (1968) reported that cottonseeds can survive floating in seawater for at least a year with undiminished viability and can thus be distributed by ocean currents. Pursegloves (1968) agreed that the most likely explanation was that cottonseeds floated across the Atlantic from Africa to South America. The development of Old World cotton as a major raw material took place in Sind. This was found during excavation in Pakistan that was dated at approximately 3000 BC (Gulati and Turner, 1928). In Peru the New World tetraploid cottonseeds dated back to 2500 BC (Hutchinson, 1959). In Southern Mexico, cotton was dated around 3500 BC (Smith, 1968). Linted cotton species have been used for cotton fabrics between 4000 and 3000 BC (Munro, 1987). The oldest archaeological remains of G. hirsutum are from the Tehuacan Valley of Mexico, 4000 to 5000 years ago (Munro, 1987).
It is assumed that G. hirsutum was probably first domesticated by pre-Columbian people of the Yucatan peninsula
(Verhalen et al., 2002). Variation determination for cotton varieties in Tanzania has been done morphologically using phenotypic descriptors. This knowledge has been important mainly for selecting parental material for crossing to improve available varieties
(Lukonge et al., 1999). Morphological properties mainly used were disease resistance, pest resistance, fibre quality, adaptability and yield components (boll size, boll number and branch number). Environment and cultivation practices had an effect on most of these morphological characteristics. Variation observed in farmers’ fields indicated a seed-mixing problem, but since the characters were unknown, it was difficult to identify individual varieties (Hau, 1997). Therefore, the objectives of this study were to characterise and quantify genetic diversity in 30 varieties collected from different areas using agronomical and morphological markers. Information obtained was compared with molecular markers in Chapter 6 to assess the relatedness between these two methods of characterisation.
(Iqbal et al., 2001; Allen and Auld, 2002). Improved cotton varieties are urgently needed to improve the cotton market through cotton yield, high ginning percentages and good cotton quality as these factors affect lint price on the world market. The success of a breeding programme is mainly due to knowledge on the available germplasm especially genetic diversity (Meredith and Bridge, 1984; Pillay and Myers, 1999). The above knowledge is important to a plant breeder.
(Farooq and Azam, 2002; Murtaza et al., 2005). DNA fingerprinting involves the display of sets of fragments from specific DNA samples. It is an effective tool to increase the speed and quality of backcrossing conversion, thus reducing the time taken to produce crop varieties with desirable characteristics
Altaf Khan et al., 2002; Rana and Bhat, 2004. With the use of molecular techniques, it is now possible to hasten the transfer of desirable genes among varieties and to introgress novel genes from related species. Using DNA fingerprinting, polygenic characteristics can be easily tagged and genetic relationships between sexually incompatible crop plants can be established .
Bruce et al., 2001.AFLP analysis has been applied in cotton to identify genes for resistance to fungal wilt diseases. It showed a greater potential compared to conventional breeding since it reduced the selection time and used small numbers of plants for detection of resistance genes.
AUison et al. (1999) estimated the trans fatty acid intake of Americans by using food intake data from the 1989-1991 Continuing Survey of Food Intakes by Individuals (CSPII) and the trans fatty acid contents of foods contained in a database compiled by the USDA. It was found that the mean percentage of energy ingested as trans fatty acids was 2.6% and the mean percentage of total fat ingested as trans fatty acids was 7.4%o (5.3 grams of trans fatty acids per day). Of this value, only 20-25% of the trans fatty acid intake comes from naturally occurring sources (basically animal fats), where as the majority of the intake comes from altered fats.
Ascherio et al. 1999.Since the 1960s, levels of trans fatty acids in margarines have declined as softer margarines have arrived on the market due to health concerns.
Lichtenstein et al. 1999 In the mid 1980s, manufactures replaced partially hydrogenated vegetable oils used in household salad and cooking oils with unhydrogenated vegetable oils (ASCN 1995). The majority of trans fatty acids consumed today come from fiied foods, margarine, snacks and baked products (Table 6). For example, a large cake doughnut has 3 g of trans fatty acids and a large order of French fries has 5 grams of trans fatty acids (Lichtenstein et al. 1999). Trans fatty acids should be Umited to no more than 3 g/day).
(UPOV, 1991; Van Esbroeck et al., 1999; Murtaza et al., 2005). This knowledge is important for germplasm collection and conservation (Pillay and Myers, 1999). Accurate morphological characterisation of varieties is an important process in breeding as variety characteristics like resistance to insect pests and diseases can be determined. For example, hairy leaf or stem varieties are resistant to insects like jassids while smooth leaf varieties reduce the trash content in harvested cotton
(Gregory et al., 1990; Pillay and Myers, 1999).
Cotton is harvested as seedcotton, which is then ginned to separate the seed and lint. The long lint fibres are processed by spinning, to produce yarn that is knitted into fabrics. The short fibres (fuzz), covering the seeds are known as ‘linters’. Delinted cottonseed can be processed to produce oil, meal and hulls. Cottonseed oil has been in common use since the middle of the nineteenth century and achieved GRAS (Generally Recognised As Safe) status under the United States Federal Food Drug and Cosmetics Act because of its common use prior to 1958 (ANZFA, 2002). Cottonseed oil is used in a variety of products including edible vegetable oils and margarine, soap and plastics. Cottonseed cake, meal flour or hulls derived from it is used in food products and for animal feed as carbohydrate roughage, but is limited by the presence of natural toxicants in the seeds (gossypol and cyclopropenoid fatty acids) (Pillay and Myers, 1999).
Brubaker et al. 1999; Cotton belongs to the order Malvales, family Malvaceae and genus Gossypium.Gossypium includes about 45 diploid (2n=2x=26) species and five allotetraploid (2n=4x=52) species (cultivated and wild)
(Meredith et al., 1997). Utilising these morphological characteristics in breeding programmes help cotton growers to obtain high yields and good fibre quality with reduced dependence on pesticides. Meredith et al. (1997) reported a higher photosynthesis rate and improved fibre quality characteristics in varieties with subokra leaves compared to varieties with normal leaves.
Morphological markers can be monitored visually without specialised biochemical or molecular techniques. Although agronomical characterisation provides useful information to users, these characteristics are normally subjected to environmental influences and must be assessed during a fixed vegetative phase of the crop.
(Jackson et al., 1998).
Accumulation of tolerance to a number of stresses is the key to wideadaptation and consequently selection in multiple environments is the best way to breed stable genotypes (Romagosa and Fox, 1993). When the effects of environmental differences are large, it may be expected that the interaction of G x E will be large. As a result it is not only average performance that is important in genotype evaluation programmes, but also the magnitude of interactions (Gauch and Zobel, 1997).
Jixiang et al. (1996) and Hussain et al. (1998); observed that ginning outturn and lint index were positively and significantly correlated with each other. Fibre strength was correlated with seedcotton yield. Tang et al.(1996) observed a high positive genetic correlation for boll weight with lint percentages, fibre strength and micronaire. Lint yield showed a genetic correlation with fibre strength and boll weight. Dedaniya and Pethani (1994) and Carvalho et al. (1995) observed that seedcotton yield per plant was positively correlated with number of bolls, plant height, boll weight, lint weight per plant and bundle strength tenacity. Negative correlation was observed among fibre strength and earliness, fibre length and fibre fineness, fibre length and fibre percentage as well as fibre fineness and fibre percentage
Bunyecha and Tamminga, 1995; Ramadhani et al., 1998
Infrastructure shortcomings severely impede the development of the cotton sector. Firstly, because most cotton must be transported by rail, the quality of rail services is vital to sectoral performance. Greater efficiency in rail transport will lower costs to growers. Secondly the road network in the Mwanza region, where most cotton is produced, requires considerable upgrading. As with rail transport, road improvements will increase efficiency and reduce costs, thereby leading to higher producer prices (Baffes, 2002).
Declining input, caused by removal of input price subsidies at farmer level, (mainly insecticides and fertilizers) led to poor quality cotton and low yields. Any quality decline due to reduced input use reflects relative prices and hence market forces .
Following reforms, as cotton prices rose in the late 1990’s, price competition and overcapacity in ginning caused abandonment of zoning, leading to the mixing of infected and uninfected seed and ultimately reduction in cotton fibre quality. The northern and southern area varieties, which were released for specific agroclimatic conditions of the area, were mixed (Government of Tanzania, 1999a; TCL and SB, 2002).
Endrizzi et al., 1985; Pillay and Myers, 1999; Iqbal et al., 2001 The entire worldwide cotton production is fromG. barbadense and G. hirsutum though G. hirsutum comprises 90-95% of the world cotton production.
In allotetraploid species, the D-genome has 13 small chromosomes and the A-genome has 13 moderately large chromosomes in the haploid complement of 26. D and A genomes differ in the amounts of moderately repetitive DNA sequences.
(Brubaker et al., 1999).; Mexican G. hirsutum types may have been grown in the Stephens Austin colony in Texas as early as 1821. Numerous introductions were probably made by soldiers returning from the Mexican-American war (1846-1848). These cultivars were subjected to strict selection to create varieties adapted to local conditions in various cotton growing regions of Northern America. Throughout these periods, outcrossing occurred between cultivars (Endrizzi et al., 1985), collectively known as American Upland cotton. The resulting high yielding and adaptable varieties were dispersed to Europe, Asia and Africa. The limited genetic diversity of cultivated upland G. hirsutum has been observed by several researchers (Multani and Lyon 1995; Iqbal et al.,1997; Iqbal et al., 2001; Lu and Myers, 2002). A hypothesis to explain this is that genetic bottlenecks occurred upon importation of small quantities of seed from Mexico to America in the 19th century. For example, Burling’s cotton in 1806 was smuggled out of Mexico in the stuffing of dolls. More bottlenecks may have occurred during the late stages of development of G. hirsutum Latifolium possibly as a result of rigorous selection (Lewis, 1962).
Meredith et al. (1997) stated that cotton yield has greatly increased since 1935 because of improved crop management and breeding. In South Africa, cotton is one of the five major crops produced commercially in the country and makes a significant contribution to the economy (Dippenaar-Schoeman, 1999).
In Tanzania, cotton is of great economical importance as it is the second most important cash crop after coffee, representing 15% of the country’s total exports and almost 40% of agricultural exports (Bunyecha and Tamminga, 1995; Baffes, 2002). Following liberalisation of the cotton industry, strong competition from village to market level resulted in the deterioration of cotton quality. Furthermore, mixing of different types of cotton varieties led to poor cotton properties (TCL and SB, 2002). Available varieties have medium yields (1200 kg/ha at research level and 300-500 kg/ha at farmers level), medium ginning percentages (36.8-39.6%) and medium fibre strength (22-25g/tex). Based on improved spinning machines, a fibre strength above 28 g/tex is recommended for international cotton fibre markets (Deussen, 1992; Hau, 1997).
(Meredith et al., 1997). Utilising these morphological characteristics in breeding programmes help cotton growers to obtain high yields and good fibre quality with reduced dependence on pesticides. Meredith et al. (1997) reported a higher photosynthesis rate and improved fibre quality characteristics in varieties with subokra leaves compared to varieties with normal leaves.
Morphological markers can be monitored visually without specialised biochemical or molecular techniques. Although agronomical characterisation provides useful information to users, these characteristics are normally subjected to environmental influences and must be assessed during a fixed vegetative phase of the crop (Swanepoel, 1999).
Tang et al. (1993a), and Baloch et al. (1996) observed positive and negative GCA effects exerted by parents on boll weight, boll number, lint yield and lint percentage. SCA effects for lint percentage observed were significant and consistent across the environment. Theoretically the presence of significant GCA and SCA in the F1 generation is a consequence of fluctuations in additive and dominance relationships among parents (Tang et al., 1993a).
Zock et al. (1995).; It has been known for years that dietary fat and cholesterol influence blood cholesterol concentrations. Extensive research has been done not only on fats as a class, but on individual fatty acids and their effects on blood lipid levels and lipoprotein concentration. The length of the chain and the degree of unsaturation of a particular fatty acid molecule contribute to the ability of the fatty acid to promote or delay the development of atherosclerosis. Scientists now agree that total dietary fat intake itself is a poor predictor of CHD risk (Nelson 1998). Small differences in fatty acid stmctures may have huge influences on their metabolic effect (Pederson 2001). For example, myristic acid (14:0) and palmitic acid (16:0) are potent cholesterol increasing fatty acids, while stearic acid (18:0) and oleic acid (cis 18:1) have no effect on semm cholesterol, and linoleic acid (18:2) decreases semm cholesterol (Pederson 2001). Laurate, myristate, and palmitate constitute the majority of saturated fatty acids consumed in the Westem diet (Nelson 1998). Trans fatty acids are metabolized in the same manner as saturated fatty acids. A study by Mensink and Katan (1990) found that consumption of trans fatty acids increases blood cholesterol levels. Other studies have shovm that saturated fatty acids and trans fatty acids are equal in their effects on blood cholesterol. Large scale epidemiological surveys and resuhs from human feeding studies all point to the same conclusion, that an increased risk from coronary heart disease is associated v^th dietary intake of trans fatty acids (Nelson 1998).
(Carvalho et al., 1995). Ibragimov (1989) observed close genetic correlation between relatively short fibre and high fibre outturn and high yield. Chen et al. (1991) observed that days from sowing to standard flowering date, days from sowing to practical flowering date, plant height and sympodia per plant were significantly positively correlated with each other and negatively correlated with first peak in cotton harvest.
Mensink and Katan, 1992; Zock et al., 1994). However, it was revealed that stearic acid (C18:0) does not raise LDL-cholesterol like other saturates and may lower the total cholesterol, thus is considered to be neutral with respect to risk of cardiovascular disease (Dougherty et al., 1995; Liu et al., 2002). On the other hand, unsaturated fatty acids, such as monounsaturated oleic acid (C18:1) and polyunsaturated linoleic acid (C18:2) and α-linolenic acid (C18:3), have the beneficial property of lowering LDL-cholesterol, thus reducing the risk of cardiovascular disease (Mensink and Katan, 1992).
Wang et al., 1989; Stanton et al., 1994.; Gossypium arboreum (A2 genome) is still grown in Pakistan and India on marginal land for use in non-woven material and is helpful in breeding programmes as a donor of host-plant resistance genes. The A-genome cotton enhances genetic diversity of tetraploid cotton breeding programmes (Stanton et al., 1994), especially with the development of techniques for introgressing A-genome germplasm into AD-genome cultivars (Stewart, 1992). Hybrids between G. hirsutum and G. arboreum have led to the selection of genotypes with earlier maturity and an increased range of fibre traits
Poehlman, 1987; Abdalla et al., 2001.; Cotton is primarily a self-pollinated crop but there is about 1-32% natural outcrossing during field cultivation that depends mainly on location and pollinator availability.
Lin et al., 1986; Becker and Léon, 1988).; Eberhart and Russell (1966) proposed the use of two stability parameters to describe the performance of a variety over an array of environments. They proposed the regression of each cultivar on an environmental index as a function of the squared deviation. Breeders search for genotypes that show a stable high yield over years and locations. In general a genotype is considered stable when its performance across environments does not deviate from the average performance of a group of standard genotypes. Eberhart and Russell (1966) proposed pooling the sum of squares for environments and G x E interactions and subdividing it into a linear effect between environments [with 1 degree of freedom (df)], a linear effect for G x E (with G-1 df) and a deviation from regression for each genotype (with E-2 df). The residual mean squares from the regression model across environments is used as an index of stability and a stable genotype is one in which the deviation from regression mean squares (S2di) is small.
Chang et al., 1978; Highly unsaturated oils are unstable when exposed to high temperatures and oxidative conditions for long periods of time. This results in the development of short chain aldehyde, hydroperoxide and keto derivatives, imparting undesirable flavours and reducing the frying performance of the oil by raising the total level of polar compounds .
Andries et al. (1971); reported that row spacing affects plant height. For such characteristics, conclusive results are obtained by repeats over years and/or locations. However, other traits like leaf colour, leaf shape and boll shape are consistent over environments and data from one or two tests normally give a good indication of relative performance
Cotton:
Cotton is the world’s most used fibre. It is cool, soft, comfortable and the principal clothing fibre of the world. Its production is one of the major factors in the world’s prosperity and economic stability. In the textiles industry more than 78% of the printed goods are of cotton fabric and it has been used for the apparel purpose since centuries. It forms the background of the world textile trades. Printing on these fabric will produce a variety of designs attractively and economically.The most commonly used thickeners for printing one cotton fabric is sodium alginate, but in view of its high price, partly substituting guar gum represents an acceptable alternative. Therefore, an attempt was made to print cotton fabric with sodium alginate and guar gum and compare its property and cost to the samples printed with sodium alginate.
Accumulation of tolerance to a number of stresses is the key to wideadaptation and consequently selection in multiple environments is the best way to breed stable genotypes (Romagosa and Fox, 1993). When the effects of environmental differences are large, it may be expected that the interaction of G x E will be large. As a result it is not only average performance that is important in genotype evaluation programmes, but also the magnitude of interactions (Gauch and Zobel, 1997).
Jixiang et al. (1996) and Hussain et al. (1998); observed that ginning outturn and lint index were positively and significantly correlated with each other. Fibre strength was correlated with seedcotton yield. Tang et al.(1996) observed a high positive genetic correlation for boll weight with lint percentages, fibre strength and micronaire. Lint yield showed a genetic correlation with fibre strength and boll weight. Dedaniya and Pethani (1994) and Carvalho et al. (1995) observed that seedcotton yield per plant was positively correlated with number of bolls, plant height, boll weight, lint weight per plant and bundle strength tenacity. Negative correlation was observed among fibre strength and earliness, fibre length and fibre fineness, fibre length and fibre percentage as well as fibre fineness and fibre percentage
Bunyecha and Tamminga, 1995; Ramadhani et al., 1998
Infrastructure shortcomings severely impede the development of the cotton sector. Firstly, because most cotton must be transported by rail, the quality of rail services is vital to sectoral performance. Greater efficiency in rail transport will lower costs to growers. Secondly the road network in the Mwanza region, where most cotton is produced, requires considerable upgrading. As with rail transport, road improvements will increase efficiency and reduce costs, thereby leading to higher producer prices (Baffes, 2002).
Declining input, caused by removal of input price subsidies at farmer level, (mainly insecticides and fertilizers) led to poor quality cotton and low yields. Any quality decline due to reduced input use reflects relative prices and hence market forces .
Following reforms, as cotton prices rose in the late 1990’s, price competition and overcapacity in ginning caused abandonment of zoning, leading to the mixing of infected and uninfected seed and ultimately reduction in cotton fibre quality. The northern and southern area varieties, which were released for specific agroclimatic conditions of the area, were mixed (Government of Tanzania, 1999a; TCL and SB, 2002).
Endrizzi et al., 1985; Pillay and Myers, 1999; Iqbal et al., 2001 The entire worldwide cotton production is fromG. barbadense and G. hirsutum though G. hirsutum comprises 90-95% of the world cotton production.
In allotetraploid species, the D-genome has 13 small chromosomes and the A-genome has 13 moderately large chromosomes in the haploid complement of 26. D and A genomes differ in the amounts of moderately repetitive DNA sequences.
(Brubaker et al., 1999).; Mexican G. hirsutum types may have been grown in the Stephens Austin colony in Texas as early as 1821. Numerous introductions were probably made by soldiers returning from the Mexican-American war (1846-1848). These cultivars were subjected to strict selection to create varieties adapted to local conditions in various cotton growing regions of Northern America. Throughout these periods, outcrossing occurred between cultivars (Endrizzi et al., 1985), collectively known as American Upland cotton. The resulting high yielding and adaptable varieties were dispersed to Europe, Asia and Africa. The limited genetic diversity of cultivated upland G. hirsutum has been observed by several researchers (Multani and Lyon 1995; Iqbal et al.,1997; Iqbal et al., 2001; Lu and Myers, 2002). A hypothesis to explain this is that genetic bottlenecks occurred upon importation of small quantities of seed from Mexico to America in the 19th century. For example, Burling’s cotton in 1806 was smuggled out of Mexico in the stuffing of dolls. More bottlenecks may have occurred during the late stages of development of G. hirsutum Latifolium possibly as a result of rigorous selection (Lewis, 1962).
Meredith et al. (1997) stated that cotton yield has greatly increased since 1935 because of improved crop management and breeding. In South Africa, cotton is one of the five major crops produced commercially in the country and makes a significant contribution to the economy (Dippenaar-Schoeman, 1999).
In Tanzania, cotton is of great economical importance as it is the second most important cash crop after coffee, representing 15% of the country’s total exports and almost 40% of agricultural exports (Bunyecha and Tamminga, 1995; Baffes, 2002). Following liberalisation of the cotton industry, strong competition from village to market level resulted in the deterioration of cotton quality. Furthermore, mixing of different types of cotton varieties led to poor cotton properties (TCL and SB, 2002). Available varieties have medium yields (1200 kg/ha at research level and 300-500 kg/ha at farmers level), medium ginning percentages (36.8-39.6%) and medium fibre strength (22-25g/tex). Based on improved spinning machines, a fibre strength above 28 g/tex is recommended for international cotton fibre markets (Deussen, 1992; Hau, 1997).
(Meredith et al., 1997). Utilising these morphological characteristics in breeding programmes help cotton growers to obtain high yields and good fibre quality with reduced dependence on pesticides. Meredith et al. (1997) reported a higher photosynthesis rate and improved fibre quality characteristics in varieties with subokra leaves compared to varieties with normal leaves.
Morphological markers can be monitored visually without specialised biochemical or molecular techniques. Although agronomical characterisation provides useful information to users, these characteristics are normally subjected to environmental influences and must be assessed during a fixed vegetative phase of the crop (Swanepoel, 1999).
Tang et al. (1993a), and Baloch et al. (1996) observed positive and negative GCA effects exerted by parents on boll weight, boll number, lint yield and lint percentage. SCA effects for lint percentage observed were significant and consistent across the environment. Theoretically the presence of significant GCA and SCA in the F1 generation is a consequence of fluctuations in additive and dominance relationships among parents (Tang et al., 1993a).
Zock et al. (1995).; It has been known for years that dietary fat and cholesterol influence blood cholesterol concentrations. Extensive research has been done not only on fats as a class, but on individual fatty acids and their effects on blood lipid levels and lipoprotein concentration. The length of the chain and the degree of unsaturation of a particular fatty acid molecule contribute to the ability of the fatty acid to promote or delay the development of atherosclerosis. Scientists now agree that total dietary fat intake itself is a poor predictor of CHD risk (Nelson 1998). Small differences in fatty acid stmctures may have huge influences on their metabolic effect (Pederson 2001). For example, myristic acid (14:0) and palmitic acid (16:0) are potent cholesterol increasing fatty acids, while stearic acid (18:0) and oleic acid (cis 18:1) have no effect on semm cholesterol, and linoleic acid (18:2) decreases semm cholesterol (Pederson 2001). Laurate, myristate, and palmitate constitute the majority of saturated fatty acids consumed in the Westem diet (Nelson 1998). Trans fatty acids are metabolized in the same manner as saturated fatty acids. A study by Mensink and Katan (1990) found that consumption of trans fatty acids increases blood cholesterol levels. Other studies have shovm that saturated fatty acids and trans fatty acids are equal in their effects on blood cholesterol. Large scale epidemiological surveys and resuhs from human feeding studies all point to the same conclusion, that an increased risk from coronary heart disease is associated v^th dietary intake of trans fatty acids (Nelson 1998).
(Carvalho et al., 1995). Ibragimov (1989) observed close genetic correlation between relatively short fibre and high fibre outturn and high yield. Chen et al. (1991) observed that days from sowing to standard flowering date, days from sowing to practical flowering date, plant height and sympodia per plant were significantly positively correlated with each other and negatively correlated with first peak in cotton harvest.
Mensink and Katan, 1992; Zock et al., 1994). However, it was revealed that stearic acid (C18:0) does not raise LDL-cholesterol like other saturates and may lower the total cholesterol, thus is considered to be neutral with respect to risk of cardiovascular disease (Dougherty et al., 1995; Liu et al., 2002). On the other hand, unsaturated fatty acids, such as monounsaturated oleic acid (C18:1) and polyunsaturated linoleic acid (C18:2) and α-linolenic acid (C18:3), have the beneficial property of lowering LDL-cholesterol, thus reducing the risk of cardiovascular disease (Mensink and Katan, 1992).
Wang et al., 1989; Stanton et al., 1994.; Gossypium arboreum (A2 genome) is still grown in Pakistan and India on marginal land for use in non-woven material and is helpful in breeding programmes as a donor of host-plant resistance genes. The A-genome cotton enhances genetic diversity of tetraploid cotton breeding programmes (Stanton et al., 1994), especially with the development of techniques for introgressing A-genome germplasm into AD-genome cultivars (Stewart, 1992). Hybrids between G. hirsutum and G. arboreum have led to the selection of genotypes with earlier maturity and an increased range of fibre traits
Poehlman, 1987; Abdalla et al., 2001.; Cotton is primarily a self-pollinated crop but there is about 1-32% natural outcrossing during field cultivation that depends mainly on location and pollinator availability.
Lin et al., 1986; Becker and Léon, 1988).; Eberhart and Russell (1966) proposed the use of two stability parameters to describe the performance of a variety over an array of environments. They proposed the regression of each cultivar on an environmental index as a function of the squared deviation. Breeders search for genotypes that show a stable high yield over years and locations. In general a genotype is considered stable when its performance across environments does not deviate from the average performance of a group of standard genotypes. Eberhart and Russell (1966) proposed pooling the sum of squares for environments and G x E interactions and subdividing it into a linear effect between environments [with 1 degree of freedom (df)], a linear effect for G x E (with G-1 df) and a deviation from regression for each genotype (with E-2 df). The residual mean squares from the regression model across environments is used as an index of stability and a stable genotype is one in which the deviation from regression mean squares (S2di) is small.
Chang et al., 1978; Highly unsaturated oils are unstable when exposed to high temperatures and oxidative conditions for long periods of time. This results in the development of short chain aldehyde, hydroperoxide and keto derivatives, imparting undesirable flavours and reducing the frying performance of the oil by raising the total level of polar compounds .
Andries et al. (1971); reported that row spacing affects plant height. For such characteristics, conclusive results are obtained by repeats over years and/or locations. However, other traits like leaf colour, leaf shape and boll shape are consistent over environments and data from one or two tests normally give a good indication of relative performance
Cotton:
Cotton is the world’s most used fibre. It is cool, soft, comfortable and the principal clothing fibre of the world. Its production is one of the major factors in the world’s prosperity and economic stability. In the textiles industry more than 78% of the printed goods are of cotton fabric and it has been used for the apparel purpose since centuries. It forms the background of the world textile trades. Printing on these fabric will produce a variety of designs attractively and economically.The most commonly used thickeners for printing one cotton fabric is sodium alginate, but in view of its high price, partly substituting guar gum represents an acceptable alternative. Therefore, an attempt was made to print cotton fabric with sodium alginate and guar gum and compare its property and cost to the samples printed with sodium alginate.
![]() |
Cotton bar |
CHARACTERISTICS OF COTTON
Cotton, as a natural cellulosic fiber, has a lot of characteristics, such as
The graph bellow shows Production and consumption of leading cotton producing countries in Millions of tones in year 2002 [5].
- Comfortable Soft hand
- Good absorbency
- Color retention
- Prints well
- Machine-washable
- Dry-cleanable
- Good strength
- Drapes well
- Easy to handle and sew
The graph bellow shows Production and consumption of leading cotton producing countries in Millions of tones in year 2002 [5].
COUNTRIES | PRODUCTION | CONSUMPTION |
US | 3.8 | 1.7 |
India | 2.5 | 3 |
Pakistan | 1.8 | 1.9 |
Turkey | 0.9 | 1.4 |
Brazil | 0.7 | 0.9 |
Indonesia | 0.4 | 0.6 |
China | 4.8 | 5.9 |
![]() |
Report |
The botanical name of American Upland cotton is Gossypium Hirsutum and has been developed from cottons of Central America. Upland varieties represent approximately 97% of U.S. production [4].
![]() |
Methodology
White cotton fabric having counts of 100 ends and 100 picks with the weight of 100 gm/m2 was selected for the study. The scouring of the fabric was done by 25 per cent soap solution at 100ºC for 1 hour. The dye used for the study was dichlorotriazinyl reactive dye. (Brill red-M). The paste of sodium alginate and guar gum were prepared separately by sprinkling the dry powder over the cold water under constant stirring and is allowed to stand for few hours to attain full swelling of the gum particles. The details of paste prepared in various concentrations are given in Table1.
After the preparation of the thickening paste, the scoured fabric was printed with the help of screen using following recipe (Kale, 1976).
- 30 Parts Procion color
- 30 Parts Urea
- 230 Parts Warm Water (120ºF-140ºF)
- 650 Parts Thickening Agent
- 60 Parts Sodium Bicarbonate
- 1000 Parts
The printing paste was prepared by mixing the dye stuff with urea before adding cold water. The mixture was heated to not more than 70ºC (160ºC) to dissolve the dye and urea. The solution obtained is then stirred into the thickening and the required amount is added to the cold printing paste. Then the paste was stirred properly and it was applied to the fabric through screen. After this the printed samples were dried and steamed for 45 minutes at 95ºC in steam ager.
Then the printed samples were subjected to visual assessment, computer colour matching bending length, crease recovery angle and cost calculation for optimisation of suitable concentration of thickening agent.
RAW COTTON COMPONENTS:
80-90% | Cellulose |
6-8% | Water |
0.5 - 1% | Waxes and fats |
0 - 1.5% | Proteins |
4 - 6% | Hemicelluloses and pectin’s |
1 - 1.8% | Ash |
During scouring (treatment of the fiber with caustic soda), natural waxes and fats in the fiber are saponified and pectin’s and other non-cellulose materials are released, so that the impurities can be removed by just rinsing away. After scouring, a bleaching solution (consisting of a stabilized oxidizing agent) interacts with the fiber and the natural color is removed. Bleaching takes place at elevated temperature for a fixed period of time [1]. Mercerization is another process of improving sorption properties of cotton. Cotton fiber is immersed into 18- 25% solution of sodium hydroxide often under tension [9]. The fiber obtains better luster and sorption during mercerization.
After scouring and bleaching, the fiber is 99% cellulose. Cellulose is a polymer consisting of anhydroglucose units connected with 1,4 oxygen bridges in the beta position. The hydroxyl groups on the cellulose units enable hydrogen bonding between two adjacent polymer chains. The degree of polymerization of cotton is 9,000-15,000 [1]. Cellulose shows approximately 66% crystallinity, which can be determined by X-ray diffraction, infrared spectroscopy and density methods.
Each crystal unit consists of five chains of anhydroglucose units, parallel to the fibril axis. One chain is located at each of the corners of the cell and one runs through the center of the cell. The dimensions of the cell are a = 0.835nm, b = 1.03 nm and c = 0.79 nm. The angle between ab and BC planes is 84º for normal cellulose, i.e., Cellulose I [8].
REPEAT UNIT OF CELLULOSE
The current consensus regarding cellulose crystallinity (X-ray diffraction) is that fibers are essentially 100% crystalline and that very small crystalline units imperfectly packed together cause the observed disorder.
The density method used to determine cellulose crystallinity is based on the density gradient column, where two solvents of different densities are partially mixed. Degree of Crystallinity is, then, determined from the density of the sample, while densities of crystalline and amorphous cellulose forms are known (1.505 and 1.556 respectively). Orientation of untreated cotton fiber is poor because the crystallites are contained in the micro fibrils of the secondary wall, oriented in the steep spiral (25-30o) to the fiber axis.
PHYSICAL PROPERTIES OF COTTON
FIBER LENGTH
Fiber length is described [7] as “the average length of the longer one-half of the fibers (upper half mean length)” This measure is taken by scanning a “beard ” of parallel fibers through a sensing region. The beard is formed from the fibers taken from the sample, clasped in a holding clamp and combed to align the fibers. Typical lengths of Upland cottons might range from 0.79 to 1.36in.
Cottons come from the cotton plant; the longer strand types such as Pima or Sea Island produce the finest types of cotton fabrics [18].
LENGTH UNIFORMITY
Length uniformity or uniformity ratio is determined as ” a ratio between the mean length and the upper half mean length of the fibers and is expressed as a percentage”[7]. Typical comparisons are illustrated below.
After scouring and bleaching, the fiber is 99% cellulose. Cellulose is a polymer consisting of anhydroglucose units connected with 1,4 oxygen bridges in the beta position. The hydroxyl groups on the cellulose units enable hydrogen bonding between two adjacent polymer chains. The degree of polymerization of cotton is 9,000-15,000 [1]. Cellulose shows approximately 66% crystallinity, which can be determined by X-ray diffraction, infrared spectroscopy and density methods.
Each crystal unit consists of five chains of anhydroglucose units, parallel to the fibril axis. One chain is located at each of the corners of the cell and one runs through the center of the cell. The dimensions of the cell are a = 0.835nm, b = 1.03 nm and c = 0.79 nm. The angle between ab and BC planes is 84º for normal cellulose, i.e., Cellulose I [8].
REPEAT UNIT OF CELLULOSE
The current consensus regarding cellulose crystallinity (X-ray diffraction) is that fibers are essentially 100% crystalline and that very small crystalline units imperfectly packed together cause the observed disorder.
The density method used to determine cellulose crystallinity is based on the density gradient column, where two solvents of different densities are partially mixed. Degree of Crystallinity is, then, determined from the density of the sample, while densities of crystalline and amorphous cellulose forms are known (1.505 and 1.556 respectively). Orientation of untreated cotton fiber is poor because the crystallites are contained in the micro fibrils of the secondary wall, oriented in the steep spiral (25-30o) to the fiber axis.
![]() |
Structure of cellulose |
FIBER LENGTH
Fiber length is described [7] as “the average length of the longer one-half of the fibers (upper half mean length)” This measure is taken by scanning a “beard ” of parallel fibers through a sensing region. The beard is formed from the fibers taken from the sample, clasped in a holding clamp and combed to align the fibers. Typical lengths of Upland cottons might range from 0.79 to 1.36in.
Cottons come from the cotton plant; the longer strand types such as Pima or Sea Island produce the finest types of cotton fabrics [18].
LENGTH UNIFORMITY
Length uniformity or uniformity ratio is determined as ” a ratio between the mean length and the upper half mean length of the fibers and is expressed as a percentage”[7]. Typical comparisons are illustrated below.
LENGTH UNIFORMITY | UNIFORMITY INDEX [%] |
Very High | >85 |
High | 83-85 |
Intermediate | 80-82 |
Low | 77-79 |
Very Low | |
Low uniformity index shows that there might be a high content of short fibers, which lowers the quality of the future textile product.
FIBER STRENGTH
Fiber strength is measured in grams per denier. It is determined as the force necessary to break the beard of fibers, clamped in two sets of jaws, (1/8 inch apart) [7]. Typical tensile levels are illustrated. The breaking strength of cotton is about 3.0~4.9 g/denier, and the breaking elongation is about 8~10%. [20]
FIBER STRENGTH
Fiber strength is measured in grams per denier. It is determined as the force necessary to break the beard of fibers, clamped in two sets of jaws, (1/8 inch apart) [7]. Typical tensile levels are illustrated. The breaking strength of cotton is about 3.0~4.9 g/denier, and the breaking elongation is about 8~10%. [20]
DEGREE OF STRENGTH | FIBER STRENGTH [g/tex] |
Very Strong | >31 |
Strong | 29-30 |
Average | 26-28 |
Intermediate | 24-25 |
Weak | |
MICRONAIRE
Micronaire measurements reflect fiber fineness and maturity. A constant mass (2.34 grams) of cotton fibers is compressed into a space of known volume and air permeability measurements of this compressed sample are taken. These, when converted to appropriate number, denote Micronaire values.
Micronaire measurements reflect fiber fineness and maturity. A constant mass (2.34 grams) of cotton fibers is compressed into a space of known volume and air permeability measurements of this compressed sample are taken. These, when converted to appropriate number, denote Micronaire values.
COTTON RANGE | MICRONAIRE READING |
Premium | 3.7-4.2 |
Base Range | 4.3-4.9 |
Discount Range | >5.0 |
COLOR
The color of cotton samples is determined from two parameters: degree of reflectance (Rd) and yellowness (+b). Degree of reflectance shows the brightness of the sample and yellowness depicts the degree of cotton pigmentation. A defined area located in a Nickerson-Hunter cotton colorimeter diagram represents each color code. The color of the fibers is affected by climatic conditions, impact of insects and fungi, type of soil, storage conditions etc. There is five recognized groups of color: white, gray, spotted, tinged, and yellow stained. As the color of cotton deteriorates, the process ability of the fibers decreases.
Work at the University of Tennessee has led to color measurement using both a spectrometer CIE-based average color measurement and a color uniformity measurement using image analysis to improve the accuracy and provide additional measurement for color grading [19]. Later the investigators developed two color grading systems using expert system and neural networks.
FIBER PROCESSING
About 30% of world cotton machines harvest production. Australia, Israel and USA are the only countries where all cottons ae picked by machines. Fifteen percent of world cotton production is ginned on roller gins and almost all rest of cotton is saw ginned in most countries [14].Cotton fibers in non-wovens are generally used in their bleached form. A lot of research and development has taken place for the efficient production of bleached fibers. The Kier bleaching process produces most of the bleached cotton fibers. Since cotton of lesser grades is useful for non-wovens, a conventional cleaning system does not suffice. This might include a coarse wire carding, called Cotton Master Cleaners, for cleaning the cotton.
The color of cotton samples is determined from two parameters: degree of reflectance (Rd) and yellowness (+b). Degree of reflectance shows the brightness of the sample and yellowness depicts the degree of cotton pigmentation. A defined area located in a Nickerson-Hunter cotton colorimeter diagram represents each color code. The color of the fibers is affected by climatic conditions, impact of insects and fungi, type of soil, storage conditions etc. There is five recognized groups of color: white, gray, spotted, tinged, and yellow stained. As the color of cotton deteriorates, the process ability of the fibers decreases.
Work at the University of Tennessee has led to color measurement using both a spectrometer CIE-based average color measurement and a color uniformity measurement using image analysis to improve the accuracy and provide additional measurement for color grading [19]. Later the investigators developed two color grading systems using expert system and neural networks.
FIBER PROCESSING
About 30% of world cotton machines harvest production. Australia, Israel and USA are the only countries where all cottons ae picked by machines. Fifteen percent of world cotton production is ginned on roller gins and almost all rest of cotton is saw ginned in most countries [14].Cotton fibers in non-wovens are generally used in their bleached form. A lot of research and development has taken place for the efficient production of bleached fibers. The Kier bleaching process produces most of the bleached cotton fibers. Since cotton of lesser grades is useful for non-wovens, a conventional cleaning system does not suffice. This might include a coarse wire carding, called Cotton Master Cleaners, for cleaning the cotton.
The conventional bleaching method for cottons meant for non-wovens is a 9 step process are:
- Fiber opening and cleaning
- Alkali scouring application
- Alkali reaction stage
- Rinsing
- Bleach application
- Bleach reaction stage
- Rinsing
- Finish application
- Drying
Finally, there is opening and bale formation.
Cotton Incorporated patented a processing line, which promised better productivity and quality. It consists of:
- Fiber opening and Cleaning
- Formation of web
- Steam purging and Alkali impregnation onto the sandwiched cotton web between 2 porous conveyors.
- After reaction, a pressure squeezing operation.
- Similar processes for bleaching and then finishing.
- Opening and Cleaning
- Conversion of fibers into a bat, weighing 10-30 ounces/sq. yard, by Needle punching or Air-lay technique.
- Scouring
- Bleaching
- Finishing
- Washing
- Drying
- Fiber opening
Visual assessment of the printed cotton sample:
Printed cotton sample were adjudge by the panel of 30 judges comprises of textile experts and research scholars for various attributes viz uniformity of colour, sharpness of outlines, whiteness of ground, overall appearance and it was observed that 8 per cent concentration of sodium alginate scored the maximum marks (384) when compared with the other ratio of sodium alginate. The sample printed with 3 per cent concentration of guar gum scored 2nd highest marks (352) whereas 2 per cent concentration and 4 per cent concentration scored 180 and 185 marks
Computer Colour Matching (Spectra Scan):
For the computer colour matching the sample printed with 6 per cent concentration of sodium alginate was taken as the standard sample and the other printed samples were compared with the standard sample. Result are presented in Table 3 which gives the DL value of the printed sample. It was found that the sample printed with the 8% concentration of sodium alginate was more closer to the standard sample with the DL* value –0.715 while the 3% concentration of guar gum had the DL value of –2.152.
Determination of the Fabric Stiffness:
Printing with sodium alginate causes a slight increase in the fabric stiffness even when sodium alginate was used as the thickening agent whereas guar gum causes slight more increase in the fabric stiffness when compared with the unprinted samples.
The statistical analysis reveals that there is insignificant (p0.05) in the stiffness value of the samples printed with various concentration of thickening agent.
Sonja S.I (2000), reported that printing with reactive dye causes a slight increase in the fabric stiffness even when sodium alginate was used as thickening agent.
Crease Recovery Angle:
There was slight decrease in the crease recovery angle when the sample was printed with sodium alginate. Printing with guar gum causes slight more decrease in the creases recovery angle when compared with the unprinted sample.
Statistical analysis of the data indicate that the difference in the value of crease recovery angle was insignificant (p0.05) when the samples were printed with various concentration of thickening agents.
Cost Calculation:
Cost was calculated for printing one metre of silk fabric by including the cost of dye, chemicals, thickeners, and excluding the labour charges. It was calculated that the fabric printed with 8 per cent concentration of sodium alginate cost Rs 22.56/- whereas printing with guar gum costs Rs 14.46/- which is about Rs 8/- less when compared with printing cost of fabric printed sodium alginate.
Selection of best concentration of the thickening agents for printing cotton fabric with reactive dye:
On the basis of various physical test of the printed sample, it is concluded that the cotton sample printed with 8 per cent concentration of sodium alginate scored the highest marks in visual evaluation, but incures more printing cost. Whereas the sample printed with the 3 per cent guar gum showed good printing results with low cost. When the results of computer colour matching were observed it was found that the results were comparable to that of sample printed with only sodium alginate (8 per cent concentration). Hence in view of price, 3 per cent concentration of guar gum is considered suitable for printing cotton fabrics. The samples were printed with the above standardised concentration of thickening agent and were tested for various physical properties, viz, tensile strength, thickness and colour fastness tests.
It was observed that there was a slight decrease in tensile strength and slight increase in the thickness of printed sample when compared to the unprinted sample. The test of colour fastness reveals that the blend of sodium alginate and guar gum in the ratio 80:20 had the excellent fastness properties towards washing, light, crocking and perspiration (Table 5)
Narker (1991), reported that reactive dyes have high tactical value, brilliancy and good allround fastness properties, particularly to rubbing (crocking) and washing.
RECENT DEVELOPMENTS IN COTTON
COLORED COTTON
Cotton fiber is dyed with chemical dyes in order to get wide range of colors. These chemical dyes and their finishing demands large amount of water in turn when these water is disposed they cause soil and water pollution. Many dyes are of chemical origin; particularly the azure ones and these are not environment friendly. Hence many countries, including India, have prohibited use of these dyes.
The negative effects of dyeing can be reduced by naturally colored cotton. This colored cotton is developed by gene transplantation. Crossing the genes from wild cotton varieties with the cultivated white ones develops this colored cotton. The research is being conducted at The University of Agricultural Sciences (UAS), Dharwad Karnataka India, to promote the cultivation of natural colored cotton. The colors that have been developed are White, Orange, Red, Yellow, Green, Purple, Brown, Blue, And Black. These negative effects of dyeing can be avoided by extensive research and growth of colored cotton. (33).
BT COTTON
Cotton requires severe pesticide in order to combat numerous pests after some years of use of pesticide by farmers these pests develop resistance to Particular pesticide. This resistance force farmers to use more amounts of pesticides. BT Cotton is developed by transgenic technique of implanting Bacillus Thuringiens bacterial gene in to cottonseeds, which makes the cotton plant and seeds resistant to majority of pests including bollworm (A. Lepidoptera), Tobacco budworm (Heliothis virescens). Bt cotton is now one of the most widely used transgenic crops. It is currently grown throughout the United States. More than 2 million acres of Bt cotton are grown in the United States alone. Other countries include China, India, and Australia. (34) According to Dept. of Agricultural and Resource Economics, University of Arizona. Bt cotton planted from 1996 to 1998 is estimated to have yielded 5% more on average than if traditional and decreased the quantity of foliar spray [35].
COTTON’S FUTURE TRENDS
The world’s cotton fiber production is approximately 89 million bales [6]. In 1997, a production forecast [6] shows that the U.S. is the largest cotton producer (18.4 million bales), followed by China (17.5 million bales), India (12.8 million bales), Pakistan (8.0 million bales) and the former U. S. S. R. republics (7.7 million bales). Other important cotton producers are Australia, Egypt, Turkey, Brazil, Argentina, Paraguay, Greece and Mexico. The highest cotton consumption is attributed to China (21.2 million bales), India (12.9 million bales) and U.S. (11.3 million bales).
SUPPLIES: The world production will increase a little bit. The 1998 U.S cotton crop is best described as a disaster due to cool wet spring in the west and inadequate rainfall in the southeast [24].
CONSUMPTION: World cotton consumption is lagging a bit behind production. After a surge in the mid-1980s, world cotton consumption has been rather flat. But the long term potential for cotton demand remains large [23].
All cotton plantings for 1999 are expected to total 14.6 million acres, 9 percent above 1998, and 5 percent greater than 1997. Upland cotton is expected to total 14.2 million acres, up 9 percent from last year. Growers planted 318,200 acres of American-Pima cotton. This is a 3% decrease from last year’s number, but 27% higher than the acreage of 2 years ago. Planting in Georgia started extremely slow due to a severely dry spring, but by June 1 was nearly on pace with average. Conversely, Texas experienced a near normal planting season although some replanting was necessary due to wind and hail damage [15].
Graph of World cotton area/World cotton yields/World cotton production/World cotton consumption [11] Graph of Cotton Prices
END USES OF COTTON:
Apparel - Wide range of wearing apparel: blouses, shirts, dresses, childrenswear, active wear, separates, swimwear, suits, jackets, skirts, pants, sweaters, hosiery, neckwear.
Home Fashion - curtains, draperies, bedspreads, comforters, throws, sheets, towels, table cloths, table mats, napkins
Conclusion
Cotton nonwovens can be recycled, re-used or disposed of by natural degradation conditions. Cotton is a readily renewable resource with long-term supply assurance. Extensive research works is improving bleached fiber quality and quantity. Nonwoven industries are producing various types of nonwovens with different manufacturing techniques, for better production. Cotton share of the textile fiber market has been steadily increasing and will continue to increase as cotton-containing items is preferred by the consumers. All the results obtained clearly indicate that the cotton samples prepared with 3 per cent concentration of guar gum produces good quality print as that of the sample printed with 8 per cent concentration of sodium alginate. Printing cost of the former sample was also low, but guar gum slightly stiffens the fabric more when compared with pure sodium alginate. Thus, from the present study it is concluded that the 3 per cent concentration of Guar Gum will be the better alternative for large-scale printing in home furnishing industries.
References :
COLORED COTTON
![]() |
Colored cotton |
The negative effects of dyeing can be reduced by naturally colored cotton. This colored cotton is developed by gene transplantation. Crossing the genes from wild cotton varieties with the cultivated white ones develops this colored cotton. The research is being conducted at The University of Agricultural Sciences (UAS), Dharwad Karnataka India, to promote the cultivation of natural colored cotton. The colors that have been developed are White, Orange, Red, Yellow, Green, Purple, Brown, Blue, And Black. These negative effects of dyeing can be avoided by extensive research and growth of colored cotton. (33).
BT COTTON
Cotton requires severe pesticide in order to combat numerous pests after some years of use of pesticide by farmers these pests develop resistance to Particular pesticide. This resistance force farmers to use more amounts of pesticides. BT Cotton is developed by transgenic technique of implanting Bacillus Thuringiens bacterial gene in to cottonseeds, which makes the cotton plant and seeds resistant to majority of pests including bollworm (A. Lepidoptera), Tobacco budworm (Heliothis virescens). Bt cotton is now one of the most widely used transgenic crops. It is currently grown throughout the United States. More than 2 million acres of Bt cotton are grown in the United States alone. Other countries include China, India, and Australia. (34) According to Dept. of Agricultural and Resource Economics, University of Arizona. Bt cotton planted from 1996 to 1998 is estimated to have yielded 5% more on average than if traditional and decreased the quantity of foliar spray [35].
COTTON’S FUTURE TRENDS
The world’s cotton fiber production is approximately 89 million bales [6]. In 1997, a production forecast [6] shows that the U.S. is the largest cotton producer (18.4 million bales), followed by China (17.5 million bales), India (12.8 million bales), Pakistan (8.0 million bales) and the former U. S. S. R. republics (7.7 million bales). Other important cotton producers are Australia, Egypt, Turkey, Brazil, Argentina, Paraguay, Greece and Mexico. The highest cotton consumption is attributed to China (21.2 million bales), India (12.9 million bales) and U.S. (11.3 million bales).
SUPPLIES: The world production will increase a little bit. The 1998 U.S cotton crop is best described as a disaster due to cool wet spring in the west and inadequate rainfall in the southeast [24].
CONSUMPTION: World cotton consumption is lagging a bit behind production. After a surge in the mid-1980s, world cotton consumption has been rather flat. But the long term potential for cotton demand remains large [23].
All cotton plantings for 1999 are expected to total 14.6 million acres, 9 percent above 1998, and 5 percent greater than 1997. Upland cotton is expected to total 14.2 million acres, up 9 percent from last year. Growers planted 318,200 acres of American-Pima cotton. This is a 3% decrease from last year’s number, but 27% higher than the acreage of 2 years ago. Planting in Georgia started extremely slow due to a severely dry spring, but by June 1 was nearly on pace with average. Conversely, Texas experienced a near normal planting season although some replanting was necessary due to wind and hail damage [15].
Graph of World cotton area/World cotton yields/World cotton production/World cotton consumption [11] Graph of Cotton Prices
![]() |
World cotton production report |
Apparel - Wide range of wearing apparel: blouses, shirts, dresses, childrenswear, active wear, separates, swimwear, suits, jackets, skirts, pants, sweaters, hosiery, neckwear.
Home Fashion - curtains, draperies, bedspreads, comforters, throws, sheets, towels, table cloths, table mats, napkins
Conclusion
Cotton nonwovens can be recycled, re-used or disposed of by natural degradation conditions. Cotton is a readily renewable resource with long-term supply assurance. Extensive research works is improving bleached fiber quality and quantity. Nonwoven industries are producing various types of nonwovens with different manufacturing techniques, for better production. Cotton share of the textile fiber market has been steadily increasing and will continue to increase as cotton-containing items is preferred by the consumers. All the results obtained clearly indicate that the cotton samples prepared with 3 per cent concentration of guar gum produces good quality print as that of the sample printed with 8 per cent concentration of sodium alginate. Printing cost of the former sample was also low, but guar gum slightly stiffens the fabric more when compared with pure sodium alginate. Thus, from the present study it is concluded that the 3 per cent concentration of Guar Gum will be the better alternative for large-scale printing in home furnishing industries.
References :
- http://www.engr.utk.edu
- http://textilelearner.blogspot.com/2012/07/production-of-cotton-fiber-from-field.html
- Wikipedia
- Cotton for Nonwovens”: A Technical Guide, Cotton Incorporated.
- Lawrence H. Shaw; ” Cotton’s Importance in the Textile Industry”, Symposium, Lima, Peru, May 12, 1998
- Tortora, P.G., Collier, B.J.: “Understanding Textiles”, 5th edition, Prentice-Hall, 1997
- “The Classification of Cotton”, USDA Agricultural Marketing Service, cotton Division, Agricultural Handbook 566, September 1995,br>
- Matthew’s “Textile Fibers, Their Physical, Microscopic and Chemical Properties”, edited by Herbert R. Mauersberger, 6th edition, John Wiley & Sons, Inc., 1954
- Gordon Cook, J.: “ Handbook of Textile Fibers, Part I. Natural Fibers”, Merrow Publishing Co. Ltd., 1968
- http://www.cottoninc.com
- http://www.sciencenews.org
No Responses to "Cotton Fiber: Cultivation to Production"