ELECTROSPINNING FOR NANO-FIBRES
Ashish Kumar Dua
M.Tech, Dept. of Textile Engineering,
Indian Institute of Technology (IIT), Delhi.
Email: ashisdua@gmail.com
Cell: +91-9560480711
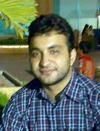
Ashish Kumar Dua
M.Tech, Dept. of Textile Engineering,
Indian Institute of Technology (IIT), Delhi.
Email: ashisdua@gmail.com
Cell: +91-9560480711
What is a nano-fiber?
- A nano-fiber is a continuous fiber which has a diameter in the range of billionths of a meter.
- The smallest nano-fibers made today are between 1.5 and 1.75 nanometers.
- At the right a human hair (80,000 nanometers) is place on a mat of nano-fibers
![]() |
Nanofibers |
![]() |
- Nano-fibers are very small which gives them unique physical and chemical properties and allows them to be used in very small places.
- Nano-fibers have a huge surface area compared to their volume
- Low basis weight
- High porosity
Surface-to-Volume Comparison:
![]() |
ABC blocks help students to understand the concept of surface to volume ratios. They need to see the additional surfaces.
Methods Producing the Nano-fibres:
Basically there are three methods:
- Drawing of Nano-fibres
- Template Synthesis
- Electrospinning
When :
- 1934 Formhals
- In the last few years the work of several researchers have made the electrospinning process suitable for the solutions of wide variety of polymers, ceramics and composite materials to produce nano-fibres.
Principle:
Construction:
It consists of four major components:
- Use of electrostatic and mechanical force to spin fibers from the tip of a fine spinneret.
- When the electrostatic Force overcomes the surface tension, a charged jet is ejected, which is then elongated in the electrostatic field. After a variety of jet destabilizations occurring simultaneously with solvent evaporation, the ultra-thinned jet is solidified and then deposited on the collector to form an overlaid nano-fibre mat.
![]() |
It consists of four major components:
- High voltage power supply
- Heating assembly (for melt- electrospinning)
- Syringe and
- Collector
High voltage power supply
- DC(more feasible) or AC
- Very high voltage (usually in the range of 10 - 30 kV)
- The polarity of the electrospinning system is arbitrary and can be reversed depending upon the polymer type and final product
1. To melt the polymer to suitable viscosity, which can be electrospun easily.
2. Various sources such as:
2. Various sources such as:
- Heating element
- Heating gun
- Laser heating
- Ultrasound heating
Syringe or capillary tube:
- Very fine capillary tube which holds the polymer melt into which a metal electrode is inserted
- It is mounted horizontally or vertically on an adjustable electrically insulating stand. A spinneret is connected to the syringe at one end for the production of nano-fibres
- A syringe pump is used to supply the polymer at a constant and controllable rate
Collector:
- Used to collect the electrospun fibres
- The collector is mounted on an insulating stand so that its potential can be controlled
- The collector may also be in the form of a rotating and translating mandrel
Process:
Important Features of Electrospinning:
Taylor Cone:
Conic angle for electrospinning PAN/DMF solutions at different PAN concentrations (wt%) under a constant electric field of 80 kVm−1
Conic angle for PAN/DMF solutions (16 wt%) under varied electric field (needle inner diameter: 0.48 mm)
Types:
Polymer
1. Effect of solution concentration on fibre morphology:
SEM micrographs of Nylon 6 electrospun fibre at a voltage of 15 kV, collector distance 8 cm for different polymer concentration (a) 15 wt.%, (b) 20 wt.% and (c) 25 wt.%
Physical properties of Nylon 6/formic acid at different concentration:
2. Effect of applied electric field:
Effect of voltage on morphology with 20 wt.% Nylon 6 polymer solution, tip to target distance 8 cm, a) 12 kV, b) 15 kV, c) 18 kV.
3. Effect of distance from tip to collector:
The wider gap allowed more time for the fluid jet to stretch and for the solvent to evaporate results in reduction of diameter.
Scanning electron microscopy (SEM) images of electrospun 20 wt.% Nylon 6 fibres obtained from formic acid solution at different collecting gap distance, (a) 5 cm, (b) 8 cm and (c) 11 cm and electric power 15 kV constantly.
- Solution is prepared by dissolving the polymer in a suitable solvent in a particular weight ratio (typically about 15 to 20% polymer)
- The solution is loaded into a syringe and the syringe is placed on a syringe pump which pumps the solution at a fixed flow rate to a needle
![]() |
- Jet initiation
- Jet thinning
- Jet stabilization
![]() |
- A high voltage is used to create an electrically charged jet of polymer solution or melt out of the syringe
- One electrode is placed into the spinning solution/melt and the other attached to the collector which is simply grounded
- The electric field is subjected to the end of the capillary tube that contains the solution fluid held by its surface tension
- This induces a charge on the surface of the liquid. Mutual charge repulsion and the contraction of the surface charges to the counter electrode cause a force directly opposite to the surface tension
- As the intensity of the electric field is increased, the hemispherical surface of the fluid at the tip of the capillary tube elongates to form a conical shape known as the Taylor cone
- Further increasing the electric field, a critical value is attained with which the repulsive electrostatic force overcomes the surface tension and the charged jet of the fluid is ejected from the tip of the Taylor cone
- The discharged polymer solution jet undergoes an instability and elongation process, which allows the jet to become very long and thin
- Solvent evaporates, leaving behind a charged polymer fiber or In the case of the melt the discharged jet solidifies when it travels in the air.
![]() |
- Suitable solvent should be available for dissolving the polymer.
- The vapor pressure of the solvent should be suitable so that it evaporates quickly enough for the fiber to maintain its integrity when it reaches the target but not too quickly to allow the fiber to harden before it reaches the nanometer range.
- The viscosity and surface tension of the solvent must neither be too large to prevent the jet from forming nor be too small to allow the polymer solution to drain freely from the pipette.
- The power supply should be adequate to overcome the viscosity and surface tension of the polymer solution to form and sustain the jet from the pipette.
- The gap between the pipette and grounded surface should not be too small to create sparks between the electrodes but should be large enough for the solvent to evaporate in time for the fibers to form.
- Higher the conductivity of the solution more charges on the surface and hence easier to stretch
- Polymers have less conductivity can be increased by the addition of the salts or electrolytes which produces ions and hence voltage required to produce smooth fibers reduces.
Solvents | Conductivity(mS/m) |
Acetone | 0.034 |
Butanol | 0.0202 |
Distilled Water | 0.447 |
Ethanol | 0.0554 |
Methano | 0.1207 |
Propanol | 0.0385 |
Dimethylformamide | 1.090 |
Taylor Cone:
![]() |
![]() |
![]() |
- Solution electrospinning and Melt-electrospinning
- In the melt-electrospinning as no solvent is used to dissolve the polymer, it is free from the problem of solvent recycling or removal
- The productivity is higher due to no loss of mass due to solvent evaporation in melt-electrospinning
- The polymers without appropriate solvents at room temperature such as polyethylene and polypropylene can be easily melt-electrospun
- Melt-electrospinning favours the production of multi-component systems such as blends and composites as in many cases no common solvent for all the components may be found
- The melt-electrospinning results the fibres, which are thicker than those produced from solution electrospinning
Polymer
- Nylon 6 and nylon 66
- Polyacrylonitrile
- PET
- PVA
- Polystyrene
- Nylon-6-co-polyamide
- Polybenzimidazole
- Polyramide
- Polyimides
- Formic Acid
- Dimethyl formaldehyde
- Trifluoroacetic acid
- Water
- DMF/Toluene
- Formic acid
- Dimethyl acetamide
- Sulfuric acid
- Phenol
1. Effect of solution concentration on fibre morphology:
- Evaporation of solvent
- Beads formation at lower cocentrtion
![]() |
Physical properties of Nylon 6/formic acid at different concentration:
Nylon Conc. (wt%) | Viscosity (pa.s) | Surface tension (mN/m) | Electric conductivity (S/cm) | Fibre Dia (nm) |
15 | 2.845 | 44.8 | .0044 | 250-700 |
20 | 3.358 | 78.5 | .00294 | 750-1200 |
25 | 4.856 | 53 | .00116 | 750-1550 |
Formic acid | .0002 | 28 | .09 |
2. Effect of applied electric field:
- Higher electric field values are obtained either through decreasing the distance between the tip and collector or by applying higher voltages.
- Increasing the electric field strength will increase the electrostatic repulsive force on the fluid results in more stretching hence slight reduction in diameter
![]() |
3. Effect of distance from tip to collector:
The wider gap allowed more time for the fluid jet to stretch and for the solvent to evaporate results in reduction of diameter.
![]() |
4. Effect of flow rate:
At the low flow rate (about 0.20-0.25 ml/hr) the electrospun fibre is cylindrical and uniform. At higher flow rates (about 0.26- 0.300 ml/hr) the fibre surface is rougher
![]() |
Applications of Electrospun Nanofibre Products:
1. Filtration:
Filter media is used to protect people and precision equipment from dust particles, smog, evaporate water, virus etc.
![]() |
- Electrospun biocompatible polymer nanofibres can be deposited as a thin porous film onto a hard tissue prosthetic device designed to be implanted into the human body. This coating film is expected to efficiently reduce the stiffness mismatch at the tissue interphase and hence prevent the device failure after the implantation
- Nanofibre, spun from compounds naturally present in blood, can be used as bandages or sutures that ultimately dissolve into body. This nanofibre minimize infection rate, blood loss and is also absorbed by the body.
- Artificial blood vessels, artificial organs, and medical facemasks.
- Nanofiber nonwoven fabric for Soft-tissue biomedical applications
![]() |
No Responses to "Electrospinning of Nanofibers | Applications of Electrospun Nanofiber Products"