DYEING OF POLYESTER AND COTTON BLEND
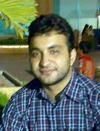
Ashish Kumar Dua
M.Tech, Dept. of Textile Engineering,
Indian Institute of Technology (IIT), Delhi.
Email: ashisdua@gmail.com
Cell: +91-9560480711
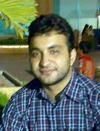
Ashish Kumar Dua
M.Tech, Dept. of Textile Engineering,
Indian Institute of Technology (IIT), Delhi.
Email: ashisdua@gmail.com
Cell: +91-9560480711
Classification of the methods for dyeing of P/C blend:
Exhaust dyeing method or batch dyeing method-
This is again classified in the following three groups-
- Two bath dyeing
- One bath one step dyeing
- One bath two step dyeing method
It is again classified in to two groups-
- Continuous dyeing-
- Pad batch process (semi-continuous)
EXHAUST DYEING:
Two bath dyeing
1. This is the process in which we have to dyed first polyester part in the HTHP beam dyeing machine or HTHP jet dyeing machine and the cotton part is dyed in the jigger machine.
2. Batch process
3. Machine used for dyeing of polyester part-
- HTHP Beam dyeing machine( First commercialized HTHP machine)
- HTHP jet dyeing machine
5. Jigger dyeing machine used
![]() |
![]() |
HTHP beam dyeing machine-
No need to explain the whole process of dyeing in beam dyeing machine. Only some important points we will discuss about it-
Advantages & features:
- Loading and unloading of the fabric is easy and time of dyeing is short.
- Dyeing in open width form.
- Most suitable for those fabrics that might crease, extend or abrade when dyed in machines where the fabric is in motion.
- Not appropriate for compact fabrics
- De-aeration is essential to avoid paler dyed spots.
- A wetting agent helps to eliminate air bubbles within the fabric roll.
- Disperse dye- X%(depends upon the shade)
- Dispersing agent-1g/l
- Sequestering agent-1-2g/l(If required)
- Defoamers -.5 to 1g/l
- Levelling agent-.5 to 1 g/l
- Wetting agent- .5g/l
- Acetic acid-enough to get ph=5-6
- Material stationary and liquor is moving.
- Batching is very important, during batching tension should be uniform and optimum.
- M:Lratio is 1:10
- Both cloth and yarn can be dyed on this machine
![]() |
Sectional diagram of a high-temperature beam dyeing machine |
- Fabric of different width can not be dyed together on a single beam.
- The dyed fabric may be display moiré effect if it is tightly due to shrinkage.
- Uneven dyeing may occur if the beam is fully loaded ,as the dye liquor has penetrate several layers of fabric.
![]() |
![]() |
The jet dyeing machine is an extension of the HPHT winch dyeing machine. Jet dyeing machine developed by BURLINGTON Industries and first machine developed in 1963 by Gaston country Machine co. of U.S.A
Features:
- Both material and liquor is moving.
- Dyeing in rope form.
- Fabric speed usually 200-250mt/min
- The jet dyeing can usually operated up to 1400c under high pressure and having capacity capable of dyeing 100 to 150 kg of fabric at a time
- Acids
- Buffers
- Sequestering agent
- Anticrease agent
- Defoamers
- Levelling agent
- Soft flow jet- slow motion of fabric. Suitable for knitted fabric
- Super jet dyeing machine- M:L is 1:1
- Aerodynamic jet dyeing machine
- Jet created by mixture of air + water
- M:L is 1:1 , drain out at a 130c
- Multi-nozzle sot flow jet dyeing machine
- Fabric of two different width can be dyed at a time so that two lots can be combined together for dyeing.
- No special batching device is required for winding the fabric as in beam dyeing.
- There is no flattening effect or uneven dyeing on the fabric as in beam dyeing
- There is possibility of entanglement of light-weight fabric during dyeing.
- Loose fibres removed from the fabric may get redeposited on the fabric surface as well as on the interior of the jet dyeing vessel, this problem does not arise in beam dyeing.
- Yarn can not be dyed in a jet dyeing machine whereas it can be dyed in a beam dyeing machine.
- Foaming problem
- Oligomers problem
- Rope marks
Jigger dyeing machine
- Open jigger or closed jigger dyeing machine-
- Closed jigger specially for vat dyeing.
- Liquor is stationary and fabric is moving.
- 500 t0 1000 meter of fabric is processed in one time.
- M:L ratio in jigger dyeing machine is about 1:5.
- Usually take 10 min. for each passage
One-bath dyeing processes ,using both the dyes such as following in the same dye bath.
- Disperse and vat dyes.
- Disperse and reactive dyes.
- Disperse and direct dyes.
![]() |
Typical dyeing recipe
- Disperse dye-X%
- Vat dye-Y%
- Dispersing agent-.5-1%
- wetting agent-.5-1%
- pH 4-5 with acetic acid (30%)
Prepare the bath with dispersing agent, wetting agent and acetic acid + treatment for 10-15min at 50-60°c then + disperse and vat + dye for 10-15min + raise temp up to 130°c in 60-90 min.
After PET part dyeing cool to 80c for proper levelling then add NaOH & Na2S2O 4 + dyeing 15min + cooling to 60°c + dyeing for 30 min. for better exhaustion Rinse with cold water + oxidation with H2O2 for 15min at 50°c + Rinsing with cold water + Soap at 95° C for 25 min using 2 g/l Lissapol D + Hot and cold rinse and then final wash off.
Only vat dyes which are stable up to 130°c can be used for this process.
One bath two step dyeing method-
All vat dyes may be used for the one –bath high temperature process provided that the dyes are finely divided enough. The IK vat dyes are not preferred because the dye liquor requires to be cooled to about 300c in order to obtain full colour yield. Therefore when IK dyes are to be used it is preferable to dye by the two-bath process.
Typical dyeing recipe-
After PET part dyeing cool to 80c for proper levelling then add NaOH & Na2S2O 4 + dyeing 15min + cooling to 60°c + dyeing for 30 min. for better exhaustion Rinse with cold water + oxidation with H2O2 for 15min at 50°c + Rinsing with cold water + Soap at 95° C for 25 min using 2 g/l Lissapol D + Hot and cold rinse and then final wash off.
Only vat dyes which are stable up to 130°c can be used for this process.
One bath two step dyeing method-
All vat dyes may be used for the one –bath high temperature process provided that the dyes are finely divided enough. The IK vat dyes are not preferred because the dye liquor requires to be cooled to about 300c in order to obtain full colour yield. Therefore when IK dyes are to be used it is preferable to dye by the two-bath process.
Typical dyeing recipe-
- Disperse dye-X%
- Vat dye-Y%
- Dispersing agent-0.5-1%
- Wetting agent-0.5-1%
- Ph-4-5(attained with 1-2 ml/l of 30% acetic acid)
Oxidation and soaping can be be achieved simultaneously using the following recipe:
- Hydrogen peroxide(35%) 1-2 ml
- Anionic detergent -.5-1g/l
- Ph-9-10
- Method is used when selected vat dyes severely. It stain PET component during high temp dyeing.
- Vat dye is added at 80°c after PET part dyeing rather than adding at the start with disperse dye.
- Except it the whole process is same as the dyeing in one bath one step.
Same as one step dyeing except the addition of reactive dye at 80°c.
This process is used for the reactive dyes which are not stable up to 130°c, due to which they can not be used in one step process
Thermosol Dyeing method:
1. PADDING
This process is used for the reactive dyes which are not stable up to 130°c, due to which they can not be used in one step process
Thermosol Dyeing method:
- continious dyeing.
- pad batch process.
- Continuous process so it gives higher production.
- Dye utilization is excellent.
- Dye can be used afterward.
- No carrier is required.
- Fabric is processed in open width form so natural feel of fabric do not get disturbed.
- No crease formation.
- Lower energy is required than batch.
- No extra heat setting is required
- Disperse dye-x g/l
- Reactive dye-y g/l
- Sodium bicarbonate or soda ash-5-20g/l
- Urea-100-200g/l
- Migration inhibitor-10-20 g/l
- Wetting agent- 1-2g/l
1. PADDING
- Padding Temp-20-300 c
- Liquor pick up-60-80%
- First partial drying in infrared pre dryer and then fully drying.
- Partial drying is done to avoid migration of dyes.
- Drying is done at 120°c.
- It is done at 180-220°c, 30-45sec
- It is the fixation step.
- Padding bath contain NaOH + Na2S2O4
- During this vat dye penetrated inside the cotton part. Then oxidation, soaping and finally washing.
One bath one step dyeing process-Disperse/Reactive dyes:
- Padding in the second step is done using NaCl + NaOH
- H- brand reactive dye is used.
- Fixation is done during steaming with saturated steam (102°c) for 30-60 sec.
- Then washing ,soaping and again washing.
- Disperse dye-x g/l
- Reactive dye-yg/l
- Sodium bicarbonate or soda ash-5-20g/l
- Urea-100-200g/l
- Migration inhibitor-10-20 g/l
- Wetting agent- 1-2g/l.
![]() |
NEW APPROACHES OF DYEING OF P/C BLEND FABRIC-
- Dyeing with Reactive Disperse Dyes in Supercritical carbon oxide.
- Dyeing of 80/20 PET/COTTON blend by using azeotropic solvent.
- Polyester/cotton blend fabric with sulphatoethyl sulphone disperse /reactive dye treatment.
- One-bath dyeing PET/COTTON blend with azohydroxypyridone disperse dye containing a fuluorosulfonyl.
Dyeing with Reactive Disperse Dyes in Supercritical carbon oxide:
What is supercritical CO2 ? - It is a naturally occurring that is chemically inert, physiologically compatible, and relatively inexpensive.
- It is nonflammable, it is supplied either from combustion process or volcanic process without the need of producing new gas & it is recycled in a closed system.
- No disposal problem.
- Easy to handle.
![]() |
- SC- CO2 act as a solvent in the range of 353-393°k temp, and 10-20 M Pa pressure
- For dyeing hydrophilic fibres like nylon, cotton- disperse dyes are not suitable for SC- CO2 dyeing.
- cotton can be dyed with fluoro triaziynyl disperse reactive dyes at 120°c in SC-. CO2
- For efficient dyeing in SC- CO2P/C blend fabric is immersed in the aqueous solution including 10% NMP( N-methyl-2-pyrrolidinone) which act as a solvent for pretreatment .
- 1% Na2CO3 + 10% NMP at room temperature for one hour + squeeze and dry at 373°K.
- When dyeing with this dye small amount of hydrogen fluoride may be formed In the reaction but Na2CO3 present in the bath does not allow hydrogen fluoride corrosion.
- This HF from dyeing solution is passed to the calcium hydroxide and recovered as calcium fluoride which is stable and harmless and present in the nature in fluorite form.
- If the same dye is uses in thermosol dyeing than-
- Homogenious dyeing is achieved in the SC-CO2 method compare to thermosol dyeing.
- L/F was better in SC-CO2
- In thermosol dye is sublime or dissolved by heating and penetrated in the fibres so the fibre is selectively dyed while in SC-CO2 dye is dissolved in the CO2 which is dissolve in the swollen fibre.
CONVENTIONAL DYEING | DYEING IN SUPERCRITICAL CO2 |
High volumes of waste water with the residual dye chemicals, etc. | No waste water at all. Dye remains as powder. No need for dispersing, leveling agents |
High-energy requirements | Only 20% energy requirement |
Dyeing/washing, drying times is 3-4 hrs per batch. | Only 2 hours. |
DYEING OF 80/20 PET/ COTTON BLEND BY USING AZEOTROPIC SOLVENT:
The blended fabric is pre-treated with the azeotropic solvent. This solvent is directly apply with pad-squeeze-dry technique.![]() |
- Disperse dye-2%
- Reactive dye-2%
- Glauber’s salt-5 gpl
- Soda ash-3 gpl
- Borax-5gpl
- Ph-10 to 11
- MLR-1:50
- Temp-80,95,1100c
- Time-30,45,60 min.
![]() |
SULPHONYL DISPERSE/REACTIVE DYES TREATMENT BY CHITIN –BIOPOLYMERS:
Conculsions:
- Pre-treated the fabric NAOH solution.
- The washing & rubbing fastness properties improved.
- The dyed sample show good rubbing within the range of colour.
- The colour strength of the dyed sample of the dyed sample increased with increase deposition of chitin on fabric.
![]() |
![]() |
Dyeing with Azohydroxypyridone Disperse dyes containing a fluorosulfonyl group- Advantages:
- It is a one-bath dyeing of PET/ cotton blends .
- alkali-clearable azohydroxypyridone disperse dyes.
- alkali-clearable azohydroxypyridone disperse dyes .containing the fluorosulfonyl group under high-temperature dyeing conditions is feasible.
- Better fastnesss properties.
- These dyes saves a lot of chemical energy.
- Excellent levelness properties.
![]() |
- One bath dyeing of Polyester/cotton blend fabrics with reactive disperse dyes in successful with SC-CO2 .The optimum dyeing temperature and pressure are about 393 K and 20 Mpa respectively . The dyeing behavior of Polyester/cotton blends is strongly affected by the dyeing characteristics of the cotton side.The colour fastness of dyed fabric is almost satisfactory ,but colour fastness become weak with a decrease in the dyeing temperature. In addition ,the colour fastness of fabric dyed in SC-CO2 is better than that with that the thermosol dyeing.
- Treatment with chitin pretreatment give the good dry rubbing and washing fastness . The alkaline pretreatment affects the greater adhesion of chitin to the surface of polyester fibres, which is manifested by the greater colour strength .Pretreatment in an alkaline solution containing 10 g/l NAOH is permitted .The greater amount of chitin used ,the worse affects are observed .
- The same effect is observed in case of azeeotropic mixture on the dyeing behaviour of 80/20 cotton blends .As the pretreatment time increased dye uptake was found increase . The slight improvement in fastness properties was also found.
- Dyeing of PET/COTTON blend with disperse dye containing the fluorosulfonyl group under high temp. dyeing conditions are feasible .Its decrease our labour cost, chemicals, energy.
- Basic Principles of Textile Coloration by Arthur D Broadbent -Professor, Université de Sherbrooke, Département de génie chimique, Faculté de génie, Sherbrooke, QC, J1K 2R1, Canada
- Dyeing of polester/cotton blends by R.B.Chavan Department of textile technology IIT Delhi
- Chemical processing of textiles-1,NCUTE
- Textile research journal Nov, 2004.
- African journal of biotechnology vol.8(6),pp.1127-1135,20March,2009
- International Scholarly Research Network ISRN Materials Science Volume 2011, Article ID 907493, 12 pages.
- Journal of the Textile Association – March-April 2007.
- Textile research division ,National research center Dokki,cairo,Egypt –Dec-2002 Fibres and polymers2008,vol 9,No2,128-133
No Responses to "Dyeing of Polyester and Cotton Blend Materials"