Automation in Weaving Process
HAFIZ ABDUL MANNAN
National Textile University, Pakistan
Phone: 0092-3236052101
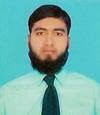
National Textile University, Pakistan
Phone: 0092-3236052101
Process automation system:
A general technology term that is used to describe any process being automated through the use of computers and computer software. Processes that have been automated require less human intervention and less human time to deliver. A process control or automation system is used to automatically control a process such as chemical, oil refineries, paper and pulp factories. The PAS often uses a network to interconnect sensors, controllers, operator terminals and actuators. A PAS is often based on open standards in contrast to a DCS (distributed control system), which is traditionally proprietary.
![]() |
Figure01: automation process cycle |
Weaving process:
Weaving is the process of interlacing two set of threads together at right angles such that they form a unified fabric4. The two sets are defined as the warp and weft, and within each set the threads lie parallel to one another. During the weaving process, the warp is defined as the set being held stationary, while the weft is the set being introduced to the warp [2].
Automation in Weaving process:
Weaving technology has seen advancements, automatic shuttle looms and automatic shuttle-less looms (e.g., Methods of holding the yarn such as rapier and the gripper) with advantages of higher productivity, to water jet and air jet looms that use water or pressurized air to transport the yarn with multiple color weft insertion. Weaving and knitting machine builders have been leading the way in utilizing computer technology in textile manufacturing for many years with their use of CAD, bi-directional communication and artificial intelligence. A CAD system can be used to develop the fabric to be produced and the design can then be transmitted over the network to the production machines to produce the desired fabric. Now, the design instructions can even be sent by modem from one country to a weaving machine located anywhere else in the world.[2]
![]() |
Figure02: Automation in Weaving |
- Automatic Pick Repair
- Automated Warp breakage Locator
- Computerized Machine Control. Manual assistance is still required for beam replacement and repair of warp breaks.
- Implementation of electronic control such as computer control in automatic looms has simplified operations as only the conditions such as yarn type and weave, width need to be input in order for the optimum operations to be performed.
Weaving is the most widely used method of fabric production for the decoration, clothing and home furnishing textile sectors. However, technical textiles, including wire cloth, are also produced on modern weaving machines.
Irrespective of the weft insertion method used, very high cycle and acceleration rates are essential for weaving machines. Furthermore, weaving machines are characterized by a large number of nonlinear motion sequences and time-critical starting times. Mechatronic solutions devised from a combination of mechanical cams and servo drives for warp let-off and fabric takeup are the modern state of the art.More recently, harness motion and weft insertion have also been implemented with individual electric drives in some instances.[3]
The demands on the automation are:
- Constant velocity relation between warp let-off and fabric take-up as a function of the main drive
- Constant thread tension during the process (uniform fabric quality)
- Weft insertion synchronized precisely with cycle times
- Fast position-oriented supply of weft threads corresponding to the color selection
- Increase in machine cycle times
- Different weft insertion processes using a projectile, airjet, or picker
- Short resetting times for lot changes
- Reproducibility of process data
- Pattern data management and preparation
![]() |
Figure 03: Operating principle of the weaving machine |
The automation solution described below offers the following advantages:
- To attain even faster resetting times, the mechanical cam can be replaced by a high resolution SIMOTION cam function for harness motions.
- The technology functions integrated in SIMOTION, particularly the electronic cam, make it easy to implement the required motion control easily and safely for the process. Furthermore, where necessary, they allow motion profiles to be modified flexibly and with minimum effort.
- Variable user interfaces enable process parameters to be quickly adapted to the execution system. These data can be reproduced at any time and assigned according to process technology. A lot change no longer requires you to make manual adjustments.
- Tools for commissioning, configuration and diagnostics integrated in the uniform, scalable SCOUT engineering system reduce service and configuration times.
The integrated automation and drives structure is rounded off by the bus-coupled dynamic SINAMICS S120 drive system and SIMOTICS S‑1FT7/1FK7 motors.
Features of the automation solution:
- Constant thread tension control during the winding and unwinding process, correct provision of thread and accurate positioning when entering the weft are closely coupled to the process control and are processed synchronously with the machine cycle. These control functions are performed by a SIMOTION D4x5‑2.
- A master that obtains its actual values from an encoder mounted on the main shaft, outputs appropriate setpoint signals to the slaves of the drive and control system.
- Coupling through an OPC interface (Ethernet) ensures operating data management and exchange of data with the pattern system.
![]() |
Figure04: Example of automation solution with SIMOTION D4x5‑2 |
With the help of computer system,we can analyze the woven sample digitized artwork instead of real fabric.We can see image disply on-screen than after making fabric. We can weave slection and sample matching on screen.
![]() |
Figure 05: Comparison between real fabric and digitized artwork |
When fabric passes through from fabric take-off to fabric beam,we can analyze the fabric faultes by X-Ray emitter.We has not to see the fabric beam by naked eye ,we can find out faultes by using automation process[4].
![]() |
Figure 06: Analyzing the fabric faults by X-Ray emitter |
We can controle one or more looms/sizing machines by our PC.we can controle our system in our room instead of go to machines.
![]() |
Figure07: Controlling one or several looms/sizing machines |
By automation process,we can analyses sketch design on computer screen as image processor.
![]() |
Figure08: Sketch jacard design process on image processor |
Comparison between manual designing and computer designing:
![]() |
Flowchart09: of manual designing and computer designing |
Figure shows when loom is runinig,we can controle our PC which things as below.
![]() |
Figure 10: Self-optimization of the weaving process |
Global competition ensures that only the fittest survive. Today’s weaver needs to ensure that he/she is able to manufacture and supply the finest quality of fabric, at the lowest cost, in the shortest possible time-frame. Automation is the only option which will allow the weaver to attain this objective.
Conclusion:
Automation has resulted in control of machines electronically from user friendly interfaces, produce intricate jacquard fabrics at the speed of commodity fabrics, inspect fabrics on loom, use optical and laser detection of warp break, reduce downtime due to higher levels of automation and quick style and warp beam change. The machine speed upto 1000 rpm is possible, 5 to 10 times faster than 20 years ago.
References :
- The Automation of Weaving: an examination of the past and future of loom design by Wendy C. Beatty Union College, 807 Union Street, Schenectady NY,
- https://eb.automation.siemens.com/mall/en/WW/Catalog/Products/10087619;sited on :08/01/2014
- http://textilelearner.blogspot.com/2013/08/automation-in-weaving-process-why-is.html
No Responses to "Automation Process in Weaving Machinery"