APPLICATION OF KNITTED FABRICS IN TECHNICAL & MEDICAL TEXTILES
Abdulwahid Dadhiwale D.K.T.E society’s textile and enginieering institute of technology Diploma In Textile Manufactures Email: wahidw202@gmail.com Abstract: Knitted fabrics and knitting technology play very important role on the fields of technical and medical textiles and their importance is ever greater. Experts estimate that their annual consumption is increasing by 3,8 % in average and it can reach about 24 million tons in 2010. Within this the consumption of each sector is increasing. Roughly one third of the world’s fibre consumption is used for production of technical textiles. The term “technical textiles” covers many fields of application that are mirrored in the terminology of Tech-textile which is very much used generally when grouping these products. Techtextil differentiates 11 groups and knitted fabrics and products made by knitting technologies can be found in each of them. The lecture introduces such applications on many examples. We think that use of knitting technologies in the development of technical and medical textiles can help this sector to survive this difficult period of the European textile industry. Keywords: knitting, knitted fabrics, technical textiles, medical textiles 1. INTRODUCTION Importance of technical textiles is great and increasing. Experts estimate that annual rising ratio of this application of textile materials is 3.8 % in average and consumption in each filed of this group of applications is anticipated as growing. Roughly one third of the quantity of the world’s fibre consumption is used in production of technical textiles. Range of technical textiles is very wide. There are various definitions of this term from which we usually use the list disseminated by the well known international fair of these products, Techtextil, which contains 11 groups.  |
Fig 1.Technical textiles |
Thus, we can say that the term “technical textiles” can be defined as do not belong to them the usual underwear and outerwear products as well as products called ordinary home textiles and household textiles (table linen, bed linen, dishcloth, curtains, etc.) except the ones used in furniture and upholstery. Most of technical textiles are made of non-conventional materials, they are usually man-made fibres, in many cases special types developed for specific applications. Metallic yarns (thin wires) alone or parallel to other yarns are also used in some technical knitted fabrics. However, traditional materials, including those of natural origin, play important role in some fields. Though each production technologies are involved in these fields, from spinning to the various kinds of fabric manufacture, including manufacture of ropes and twines, we concentrate in this paper to the role of knitting technologies.
2. USE OF KNITTING TECHNOLOGIES IN MANUFACTURE OF TECHNICAL TEXTILES
Studying the objects exhibited on fairs and the articles published in technical papers and on the Internet we have the experience that various kinds of warp knitted fabrics play the most important role among knitted technical textiles. These fabrics are made on tricot, raschel, crochet and knit braiding1 machines. Products of these machines can be used in themselves, like nets or bandages, but also as reinforcement materials in composites or backing materials for laminated or coated fabrics. However, besides warp knitting technology important products are made also on weft knitting, mainly on circular knitting machines but V-bed flat knitting must not be neglected either. 2.1 Nets Application field of nets is extremely wide. Agriculture, fishing, packaging, transport, sports, shading technology, construction, healthcare, surgery, safety technology and military presents many good examples for that. Many of these nets are made by raschel or crocheting technology the great advantage of which is that they do not contain knots (Fig. 2). This makes the nets easier to handle because the layers do not tangle up and there are no knots that could harm the good packed into the net. Warp knitted nets – both flat and tubular ones – can be produced with very high productivity. Materials used for net manufacture are very different, depending on the end use. Spun yarns or filament yarns, narrow plastic tapes are commonly used for this purpose. Elastic nets are made with using of elastane yarns. 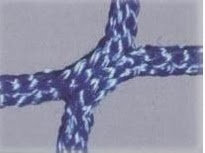 |
Figure 2: Raschel net does not contain knots |
Width of flat nets knitted on raschel or tricot machines may reach as well 5 to 6 metres while to make narrower variants (up to 100 to 120 cm width) crochet machines are also available. Raschel machines with two needle bars are able to produce wide tubular net fabrics. To manufacture tubular nets of smaller diameters (from 1 or 2 centimetres to about 20 cm) knit breading machines can be used very effectively but their final diameter can be extended in the practice if they contain elastane yarns. 2.2 Knitted fabrics with orientated behaviours Knitted fabrics with orientated behaviours are made usually with lots of yarns laid lengthwise, crosswise and/or diagonally into the fabric. Their keeping together is performed by warp knitted loops. Aim of these 1 Knit braider is a circular warp knitting machine working with latch needles, making similar products as braiding machines (nets, twines, etc.) a) b) c) 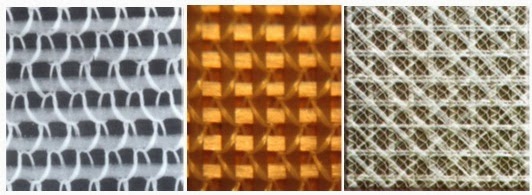 |
Figure 3: Knitted fabrics with orientated behaviours |
a) Monoaxial [5], b) biaxial, c) multiaxal [5] structures is mainly to reduce the stretch and/or to increase the forth of the fabric in one or more directions. If this effect is realized only in one direction (lengthwise or crosswise) the fabric is called “unidirectional” or “monoaxial”. If this behaviour asserts itself in both directions the fabric is called “biaxial”. “Multiaxial” or “multidirectional” fabrics have almost the same behaviour in every direction (Fig. 3.). To manufacture such fabrics special tricot and raschel machines have been developed completed by equipment to prepare and lead the lots of reinforcing yarns into the place of loop formation. In these fabric constructions the laid-in yarns play the main role, the loops only link them together. There are a great number of end uses for these fabrics. Biaxial fabrics with PVC coating, for instance, are used for manufacture of stressed roof constructions by which very wide spaces can be covered. Fabrics with directed behaviours are available also as reinforcement materials of composites or for geogrids. 2.3 Spacer fabrics Among knitted fabrics perhaps the most spectacular development can be registered in case of spacer fabrics. This is already the product of the 21st century, their development began only several years ago but it has made great progress since then. Though the principle of the fabrication is not new, it goes back to the manufacture of plush fabrics on raschel machine, the adaptation of this technology to make a completely new type of fabric is very ingenious. At the beginning they were developed really on two needle bar raschel machines but now there are also circular knitting machines on the market for manufacturing of such products and, of course, V-bed flat knitting machines are also able to make spacer fabrics of some kinds (Fig. 4). The two surface layers of spacer fabrics are usually linked by relatively thick monofilaments which makes the fabric elastic when pressed in thickness direction. This is the most important reason why spacer fabrics have found many fields of application. They can substitute foam in seats or beds, in orthopaedic support devices, in bras and shoes. It can serve in smart clothes as heat insulation or for forming of ventilation passages. As a type of geotextiles spacer fabrics can be used to lead off water from the soil. In manufacturing of composites used in the motor industry or ship building they can work as reinforcement inlay. Using proper yarns or with application of special treatment they can be electrically conductive, flame retardant, antibacterial, etc. As we see at this moment, most spacer fabrics used are made on raschel machines or, in recent times, also on crochet machines. Needle bed distance on these machines can be varied within wide range and fabric thickness can reach even 60 mm. On circular knitting machines needle bed distance is much more limited, only thinner (thickness of some millimetres) spacer fabrics can be made on them. However, these variants are also very important and can be found in many products. I am convinced that spacer fabrics will have high importance in the future among technical end uses,including healthcare. a) b) c) a) Raschel [5], b) circular knitted [4], c) V-bed flat knitted [3] 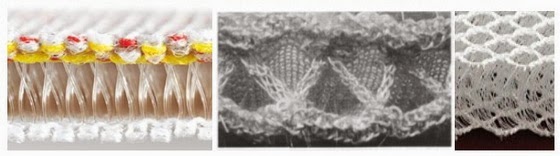 |
Figure 4: Spacer fabrics |
2.4 Stitch bonding Stitch bonding machines combine knitting and sewing. They have grown from warp knitting technology and their products occupy an intermediate position between knitted and nonwoven fabrics. This fabric contains a carded web which is reinforced by yarns or loops formed from fibres pulled out from the web itself. Needles of the warp knitting machine pierce holes through the web and work like a sewing needle when forming a seam of chain stitching (called pillar stitch in warp knitting technology) or zigzag seam where stitches made on neighbouring needles couple with each other (called tricot lap in warp knitting technology). These fabrics have great importance in almost each class of technical textiles. They are used very often as reinforcing materials in composites or for heat or sound insulation, filling materials in clothes or furniture, etc. A further variant of such fabrics is when not only carded web but lots of yarns are laid in various directions over the web and all of these are stitched together. This formation may be called “composite fabric” since it is a composition of various types of textiles (web and yarns). They find application fields among filters, geotextiles, reinforcement materials in composites, etc. Advantage of these fabrics is that the carded web may be made of various fibres which, because of their length or quality, can not be spun, even in various blending, fabric thickness and stitch density (number of stitches in length unit) as well as yarn counts (in accordance with machine cut) can be varied in relatively wide range. The fabric can be easily formed. At the end of its lifetime it can be torn and recycled. 2.5 Knitted fabrics in construction Construction industry is a great market for textiles and also for knitted fabrics among them. Around buildings being under construction or renovation the scaffold is usually covered by raschel-knitted net (Fig. 5) made of polypropylene foil tapes. Knitted fabrics can be used also to reinforce wall coverings, both outside and inside. Some types of geotextiles and geogrids are also knitted structures, as mentioned above (Fig. 6) Many buildings, and not only provisional ones, have roofs made of textile fabrics (sports stadiums, air terminals, halls for various functions, etc.). If this roof is made from knitted fabric bi- or multiaxial knitted structures are used with waterproof and weatherproof coating. Huge areas, many hundreds of square metres can be covered by such fabrics. 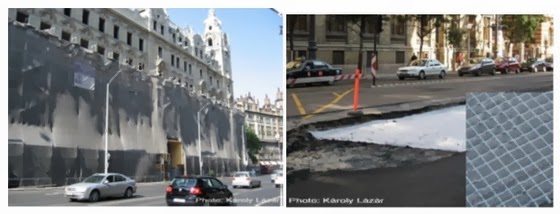 |
Figure 5 and 6: Scaffold covered by raschel net and Knitted composite fabric used for driveway reinforcement |
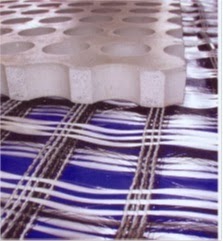 |
Figure 7: Warp knitted fabric for reinforcment of concrete slab [2] |
Another possible application of knitted fabrics in construction is textile reinforced concrete. There are warp knitted structures developed especially for this purpose like the one shown in Fig. 7. Textile reinforced concrete has the advantage that it is much lighter than the one reinforced by steel bars. 2.6 Knitted fabrics in medical treatment Many kinds of textiles are used in medical treatment. It is not surprising that a great part of clothing worn by doctors and nurses in hospitals and clinics is product of the knitting industry (e.g. undershirts, socks). But sometimes they are not conventional ones, they are made from yarns or with finishing that make them antibacterial against infections or against of rising of unpleasant sweaty smell. Various types of bandages (both rigid and elastic), surgical stockings, certain parts of orthopaedic equipment (ortheses) (like knee-, wrist- and elbow-braces, calf and lumbar supports, etc.) are also made by knitting technology. An important application field for spacer fabrics is manufacturing of mattresses for beds, operating tables and wheelchairs. Knitted products find application field also among implants: artificial blood vessels (they can be circular knitted or warp knitted, the latter is made on double needle bar raschel machine and can be made also in Y form), surgical meshes (made on tricot machine), coverings of artificial heart valves, etc. (Fig. 8). Thus, development and application of textiles open interesting possibilities for medical sciences and vice versa: manufacture of textiles for medical treatments offer important possibilities for the textile industry. Cooperation of doctors and technical experts of the textile industry can lead to development of new surgical technologies. Structure of the textiles used as implants is determined by its material composition, fibres’ behaviour and features of degradation. Materials of sutures and implants having biologically good properties, designable absorption and degradability and that endure the sterilization process are continuously subjects of research. At the same time, continuous development of textile technologies and machines enables to develop newer and newer methods in surgery and medical treatment. For this mutual development textile technologists and doctors must closely cooperate, while all the administrative procedures concerning manufacturing and trading of such products must be strictly respected.
2.7 Knitted fabrics in functional clothes Knitted fabrics may be important components of functional clothes, too. For example, spacer fabrics can be used here as lining that, due to its hollow structure, enables ventilation inside the garment or, due to its elastic behaviour in thickness direction, protects against pressure or hit. This is why this fabric is a penchant for lining of motorcyclists’ protective garments. The speciality of a spacer fabric that there is a distance between its two surfaces but they can be springily pressed together enables to use them as electric switch if electrically conductive yarns are used in the two isolated surfaces. When they connect to each other under pressure an electric signal can be created. Also pressure sensor can be built in between the surfaces. Cables can be led in the inside hollow. Undershirts, trousers, socks made from elastic knitted fabrics fit close to the body and if sensors are fastened on them they can transport signals of the movements and the state of the body (perspiring, pulse, breath frequency, etc.). Remarkable developments are going on – also in Hungary – with knitted fabrics containing metallic fibre components for manufacture of protective underwear against electromagnetic radiation as well as with other types of underwear that contain modacrylic or carbon fibres to make the knitted garments flame retardant. Socks made from heat resistant aramide fibres do good service on hot workplaces. On the recent Technical textile in 2009 a knitting factory presented a complete set of knitted underwear (long-sleeve shirt, trousers, socks, a) b) c) 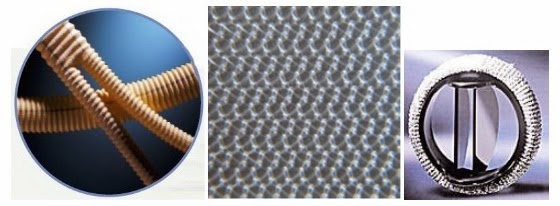 |
Figure 8: Knitted implants |
a) Artifitial blood vessel [6], b) surgical mesh [8], c) artificial heart valve [7] hood) made of a special blending of modacrylic, aramide and cotton fibres to be worn in hot work environment. An other set of knitted underwear was made of antistatic polyester completed by antibacterial treatment. 3. CONCLUSIONS All of these examples prove that there are very many possibilities for the European knitting industry to renew. Hungary has established, under the umbrella of the Hungarian Society of Textile Technology and Science, the National Technology Platform for Renewal of the Textile and Clothing Industry (TEXPLAT), joining the Technology Platforms created by the European Union. Aim of the European Union with this initiative was to strengthen the research and development activity and to speed up the realization of results of innovation in order to react successfully to the challenge of global competition. One of these European Platforms is the European Technology Platform for the Future of the Textile and Clothing Industry (ETP-FTC) – this is the background of the Hungarian project. Within this project the Hungarian Society of Textile Technology and Science prepared in 2009 a Strategic Plan for the research, development and innovation of the Hungarian textile and clothing industry. In this plan all the possible scopes of development were examined and evaluated. Many proposals have been formulated also for the knitting industry, most of them are in connection with the subjects expounded above. Our opinion and the proposals have been collected in a study presented to the concerning government office, calling the officials’ attention to the aspect that the Hungarian textile and clothing industry could chose a completely new way for developing and it must not be considered as subject of write-off. The next step is going on this year: we have to discuss with entrepreneurs what can be really put into practise from our proposals. They are in difficult position nowadays, the Hungarian economy is not on the top and only few companies of the textile and clothing industry are able to invest new technology. However, there are also good examples and we do hope that some of the possible solutions will be realized in the near future. 4. REFERENCES - AVR – Allgemeiner Vliesstoff-Report, 2007. No. 3.
- Liba – New double needle bar knitting machine for technical textiles. Melliand International, 2008. No. 2. p. 105
- Kanakaraj, P.; Anbumani, N.: 3D knitted spacer fabrics and their application. Melliand International, 2007. No. 1. pp. 47–52.
- http://www.mayercie.de/en/news/43_1687.htm Accessed: 2009-01-27
- Karl Mayer’s leaflets
- www.goremedical.com/en/file/73641.pdf Accessed: 2009-04-09
- http://www.ismaap.org/81.0.html Accessed: 2009-04-06
- http://www.tmte.hu/11kiadvanyok/111matete/111_2009_04_pdf/133_Techtextil.pdf Accessed: 2010-02